A aplicación da tecnoloxía de prototipado rápido no lanzamento de investimentos
O prototipado rápido (RP) é unha tecnoloxía de alta tecnoloxía desenvolvida nos anos noventa. Pode converter rapidamente os conceptos de deseño na mente das persoas en obxectos reais. É especialmente digno de mención que todo o proceso de desenvolvemento do produto non require ningún molde nin equipo de proceso, o que acorta moito o ciclo de produción de prototipos e novos produtos e convértese rapidamente nun importante medio e ferramenta para mellorar a competitividade das empresas. A enquisa por cuestionario de Internet publicada por INCAST 1990 (2004) mostra que máis do 11% de máis de 93 fabricantes de fundición de investimento en Europa empregaron prototipos rápidos. Todos os entrevistados coinciden en que o uso desta nova tecnoloxía é esencial para acelerar novos produtos. É moi importante desenvolver e mellorar a capacidade das empresas para responder rapidamente ao mercado.
A aplicación de métodos comúns de prototipado rápido no lanzamento de investimentos
A aplicación da tecnoloxía de prototipado rápido na fundición de investimento inclúe principalmente os seguintes aspectos:
1. Fai un investimento
Ao facer patróns, a máquina de facer prototipos rápidos non só pode introducir modelos xeométricos tridimensionais establecidos por outros programas CAD, senón tamén recibir ficheiros de datos escaneados por CT industrial (Tomografía por ordenador). Por exemplo, primeiro escanee a peza (hélice de rosca, Figura 12-1a) a través de CT para obter unha imaxe bidimensional da súa sección transversal (Figura 12-1b). Posteriormente, o software de procesamento de imaxes combina as imaxes bidimensionais de cada sección (Figura 12-1c) para formar un modelo xeométrico tridimensional (Figura 12-1d). Despois envialo á máquina de prototipado rápido para facer un patrón (Figura 12-1e) [2]. Este método de enxeñaría de restauración (inversa) non só pode restaurar pezas da máquina, senón tamén imitar certos órganos humanos.
2. Fabricación de moldes (moldaxe por compresión) e outros equipos de proceso
Existen dous métodos para fabricar moldes de fundición de precisión mediante prototipado rápido: un é primeiro fabricar un molde mestre e despois refacer perfís de goma epoxi ou silicona; o outro método é empregar o bloque de perfilado tridimensional xerado no sistema CAD. O modelo xeométrico introdúcese directamente na máquina de facer prototipos rápidos para facer molduras de resina. Este tipo de perfís é axeitado principalmente para a produción de lotes pequenos (decenas de pezas). Se se pulveriza unha capa de metal de aproximadamente 2 mm de grosor sobre a superficie do molde mestre e a continuación enchese resina epoxi para facer un perfil composto metal-epoxi, pode cumprir os requisitos de producir centos de pezas fundidas de precisión. Cando se usa o método SLS, por exemplo, o obxecto de procesamento cambia de po de resina a po de aceiro cunha delgada capa de resina termoendurecible na superficie, sinterizado por láser para formar un compacto e logo disparado para eliminar a resina e, finalmente, líquido de cobre infiltrase nos poros do compacto. O perfilado resultante é similar ao metal en termos de resistencia e condutividade térmica. Ademais, a tecnoloxía de prototipado rápido tamén se pode usar para fabricar certos moldes de forma irregular.
3. Produción directa de pezas fundidas de moldes
A principios dos anos 1990, o Laboratorio Nacional Sandiana nos Estados Unidos realizou un estudo especial chamado Fast Casting (FastCAST), que recibiu o nome de Direct Shell Casting (DSPC). Desafortunadamente, hai moi poucos informes máis tarde.
En 1994, Z Corporation dos Estados Unidos desenvolveu con éxito a tecnoloxía de impresión 3D Impresión 3D. A tecnoloxía foi orixinalmente inventada e patentada polo profesor Ely Sachs do Instituto Tecnolóxico de Massachusetts. O principio básico é similar ao método SLS. En primeiro lugar, pulverízase cun rodillo unha capa de material refractario ou po de plástico. A diferenza con respecto ao SLS é que, en vez de conducir un cabezal emisor de láser, conduce un cabezal de impresión inxección de tinta para pulverizar cola para "imprimir" segundo a forma da sección transversal do produto. Repita as accións anteriores ata completar as pezas, polo que se denomina "tecnoloxía de impresión 3D". As súas vantaxes son baixos custos operativos e materiais e alta velocidade. Se o po pulverizado é un po mixto de xeso e cerámica, pódese converter directamente e rapidamente nun molde (molde de xeso) para fundir aluminio, magnesio, cinc e outras pezas fundidas de aliaxe non ferrosa, chamado ZCast (Figura 12-2) .
A comparación dos efectos de aplicación de métodos de prototipado rápido de uso común
Na actualidade, os métodos de prototipado rápido máis populares na produción real inclúen litografía tridimensional (SLA), sinterización selectiva por láser (SLS), deposición por fusión (FDM), fabricación de laminados (LOM) e fundición directa de moldes (DSPC)). Nos últimos anos, moitas institucións de investigación estranxeiras compararon os métodos anteriores en termos de calidade dos patróns de produción e rendemento no lanzamento de investimentos. Os resultados son os seguintes:
- 1) O método SLA ten a maior precisión dimensional do patrón, seguido de SLS e FDM, e o método LOM é o máis baixo [4].
- 2) Rugosidade superficial do patrón A superficie do patrón está pulida e acabada e mídese cun medidor de rugosidade superficial. Os resultados móstranse na táboa 12-1 [4]. Pódese ver que a rugosidade superficial é máis fina polos métodos SLA e LOM, e o método FDM é o máis groso.
- 3) A capacidade de reproducir pezas finas A capacidade destes catro métodos para reproducir pezas finas investigouse cun bastidor cun paso dos dentes duns 3 mm como obxecto. Como resultado, SLA é o mellor e FDM é o peor [4].
- 4) Rendemento na fundición de investimento Entre os catro métodos anteriores, o produto en si é un método de molde de cera (como FDM ou SLS), que pode adaptarse facilmente aos requirimentos do proceso de fundición de investimento e, sen dúbida, ten un mellor rendemento. Aínda que tamén se poden queimar patróns de resina ou papel, non son tan fáciles de adaptar aos requirimentos de fundición como os moldes de cera. Precísanse melloras continuas para evitar desvantaxes.
Comparación da rugosidade superficial dos patróns
Parte de medición | OOM | SLS | FDM | SLA |
Avión de nivel | 1.5 | 5.6 | 14.5 | 0.6 |
Avión inclinado | 2.2 | 4.5 | 11.4 | 6.9 |
Plano vertical | 1.7 | 8.2 | 9.5 | 4.6 |
Desde o punto de vista xeral, aínda que o método SLA ten certa incompatibilidade co proceso de fundición de investimento, é popular pola súa boa precisión dimensional e calidade superficial. En países estranxeiros, especialmente nas industrias aeroespacial e militar, as empresas de fundición de investimentos son moi empregadas. Aínda que a calidade do método SLS é lixeiramente inferior á do SLA, é fácil adaptarse aos requirimentos do proceso de fundición de investimento. Polo tanto, cada vez son máis as aplicacións que se utilizan na fundición de investimentos nacionais. Aínda que o método FDM é o máis sinxelo para adaptarse aos requirimentos do proceso de fundición de investimento, a precisión dimensional e a calidade da superficie dos moldes de cera non son satisfactorios; mentres que o método LOM é de calidade aceptable, pero é difícil adaptarse ao investimento. Polo tanto, é difícil adaptarse ao casting de investimento. A promoción e aplicación dos dous métodos no casting de investimento están suxeitos a certas restricións.
Novos desenvolvementos na aplicación de SLA e SLS en fundición de investimentos
1. Nova resina fotopolimerizable
O método SLA comercializouse xa en 1987. Empregouse orixinalmente para facer modelos físicos e prototipos con certas funcións. A principios dos anos 1990, o software QuickCast de 3D System Inc nos Estados Unidos desenvolveuse con éxito, permitindo á máquina de prototipado rápido SLA producir unha estrutura en forma de panal (Figura 12-3a) mantendo un aspecto suave e denso (Figura 12 -3b), non só aforra o 90% dos materiais de moldaxe, senón que tamén cando se dispara a casca, o patrón primeiro cae cara a dentro sen rachar a casca. Ademais, a xente descubriu gradualmente que para as resinas fotopolimerizables para a fabricación de moldes tamén necesitan cumprir os seguintes requisitos especiais:
- Viscosidade: se a viscosidade da resina é demasiado alta, será difícil drenar a resina restante na cavidade despois de que se faga o patrón. Se hai moita resina residual, aínda pode rachar a cuncha durante a cocción, polo que a miúdo é necesaria unha separación centrífuga. Medidas. Ademais, a superficie do patrón acabado tamén é difícil de limpar.
- A cinza residual é quizais o requisito máis importante. Se a cinza residual despois de cocer a cuncha provocará inclusións non metálicas e outros defectos na superficie da fundición.
- · Contido de elementos de metal pesado: isto é particularmente importante para a fundición de superaleacións. Por exemplo, o antimonio é un elemento relativamente común nas resinas fotopolimerizables SLA. Se aparece na cinza residual despois de disparar a cuncha, pode contaminar a aliaxe e incluso provocar o desfeito da fundición.
- Estabilidade dimensional: o tamaño do patrón debe permanecer estable durante toda a operación. Por esta razón, a baixa absorción de humidade da resina tamén é moi importante.
Nos últimos anos, DSM Somos dos Estados Unidos desenvolveu con éxito un novo tipo de resina fotopolimerizable Somos 10120, que cumpre os principais requisitos mencionados e é bastante favorecida polos fabricantes de fundición por investimento. Este novo produto foi fundido en tres plantas de fundición de precisión diferentes en tres aliaxes (aluminio, titanio e aliaxe de cobalto-molibdeno) e obtivo resultados satisfactorios.
2. Use o modelo SLA para a produción de lotes pequenos
Hai dúas cuestións principais que hai que ter en conta na produción en pequeno lote de pezas fundidas de precisión mediante patróns SLA: unha é a precisión dimensional que o patrón e a fundición poden acadar e a outra é se o custo de produción e o tempo de entrega teñen vantaxes. Varias plantas de fundición de precisión nos Estados Unidos, como Solidiform, Nu-Cast, PCC e Uni-Cast, utilizaron patróns SLA para lanzar centos de pezas fundidas. Despois da medición real do tamaño da fundición, a análise estatística mostra que se emprega a nova resina fotopolimerizable 11120 desenvolvida por DSM Somos. Coa tecnoloxía QuickCast, o patrón SLA resultante ten unha desviación de tamaño non superior ao 50% do valor de tolerancia de fundición. O tamaño da maioría das pezas fundidas cumpre cos requisitos de tolerancia e a taxa de aprobación é superior ao 95% (Figura 12-4) [7].
Aínda que o custo de facer un patrón SLA é moito maior que o de facer o mesmo molde de cera e leva máis tempo, pero non é necesario deseñar e fabricar o perfilado. Polo tanto, cando se produce unha soa peza en pequenos lotes, o custo e o tempo de entrega aínda son vantaxes. Canto máis complexo é o casting, máis evidente é esta vantaxe. Tome como exemplo a fundición de precisión de aviación en forma complexa producida por Nu-Cast (Figura 12-5) [7], o custo de fabricación do molde é de aproximadamente 85,000 dólares estadounidenses, prodúcense 4 moldes de cera ao día e o custo de cada cera molde (incluídos materiais e man de obra) 150 USD. Se se adopta o método SLA, cada modelo SLA custa 2846 dólares estadounidenses, pero non é necesario deseñar e fabricar moldes. A partir deste cálculo, se a produción é inferior a 32 pezas, o custo do uso de moldes SLA é inferior ao dos moldes de cera; se hai máis de 32 pezas, o custo é superior aos moldes de cera (Figura 12-6); usando moldes de cera, leva 14-16 semanas deseñar e fabricar moldes. E o molde SLA non precisa de molde. Polo tanto, se a produción é inferior a 87 pezas, empregando moldes SLA, a entrega de pezas fundidas é máis rápida que os moldes de cera (Figura 12-7). Pero máis de 87 pezas, o molde de cera é máis rápido [7]. Outro factor que hai que ter en conta é que se se usa un molde de cera, cando se actualiza o produto, hai que volver a facer o molde, o que custa; mentres que co aspecto SLA, todo o que hai que facer é cambiar o modelo xeométrico CAD, que é moito máis sinxelo e rápido que volver a facer o molde. .
3. Patrón de cera impregnada en po de poliestireno sinterizado
SLS utilizou inicialmente un láser para sinterizar un po de cera especial nun molde de cera, que é moi axeitado para as características do proceso de fundición de investimento. Xa a finais de 1990, había máis de 50 fundicións nos Estados Unidos, producindo uns 3000 moldes de cera e fundíndoos con éxito. Produce unha variedade de pezas fundidas de metal. Non obstante, o po de cera non é o material de moldaxe máis ideal. A resistencia do molde de cera feito a partir del é insuficiente e é fácil suavizarse e deformarse cando a temperatura é alta e é fácil romper cando a temperatura é baixa. Polo tanto, a principios dos anos 1990, algúns usuarios de SLA nos Estados Unidos intentaron substituír o po de cera por pos termoplásticos como o poliestireno (PS) ou o policarbonato (PC). Este tipo de material faise unha forma solta e porosa (a porosidade é superior ao 25%), o que reduce o risco de inchazo e rachamento da cuncha durante o desmoldado. Despois de disparar a cuncha, o contido de cinzas é menor, pero a superficie do patrón é rugosa. Polo tanto, despois de que se faga o patrón, é preciso enceralo e pulilo á man para facer a superficie lisa e densa. Na actualidade, este método foi moi empregado no país e no estranxeiro.
Mantén a fonte e o enderezo deste artigo para reimprimilos:A aplicación da tecnoloxía de prototipado rápido no lanzamento de investimentos
Minghe Casting Company dedícase á fabricación de pezas de fundición de alta calidade e de alto rendemento Fundición a presión de parede delgada,Fundición a cámara quente,Fundición a cámara fría), Servizo redondo (servizo de fundición a presión,Cnc mecanizado,Fabricación de moldes, Tratamento de superficie). Calquera requirimento de fundición a presión de aluminio, magnesio ou fundición de Zamak / cinc e outros requisitos de fundición son benvidos para poñerse en contacto connosco.
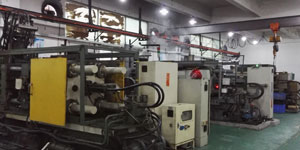
Baixo o control de ISO9001 e TS 16949, todos os procesos lévanse a cabo a través de centos de máquinas de fundición a presión avanzadas, máquinas de 5 eixes e outras instalacións, que van dende as blasters ata as lavadoras Ultra Sonic. Minghe non só ten equipos avanzados senón que tamén ten profesionais equipo de enxeñeiros, operadores e inspectores experimentados para facer realidade o deseño do cliente.
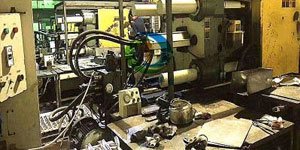
Fabricante por contrato de pezas fundidas. As capacidades inclúen pezas de fundición de aluminio a cámara fría de 0.15 libras. ata 6 libras, configuración rápida de cambio e mecanizado. Os servizos de valor engadido inclúen o pulido, vibración, desbarbado, granallado, pintura, revestimento, revestimento, montaxe e ferramentas. Entre os materiais traballados inclúense aliaxes como 360, 380, 383 e 413.
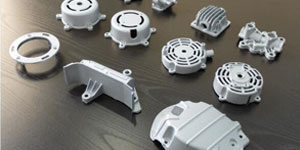
Servizos de enxeñaría simultánea de asistencia ao deseño de fundición por cinc. Fabricante a medida de pezas de fundición de cinc de precisión. Pódense fabricar pezas fundidas en miniatura, pezas fundidas de alta presión, pezas de molde de varias diapositivas, pezas de molde convencionais, pezas de moldaxe de pezas individuais e pezas de fundición independentes e pezas de fundición seladas. As pezas fundidas pódense fabricar en lonxitudes e anchuras de ata 24/0.0005 polgadas +/- XNUMX polgadas de tolerancia.
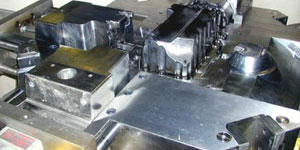
Fabricante certificado ISO 9001: 2015 de magnesio fundido a presión, as capacidades inclúen fundición a presión de magnesio de alta presión ata cámara quente de 200 toneladas e cámara fría de 3000 toneladas, deseño de ferramentas, pulido, moldeado, mecanizado, pintura en po e líquido, QA completo con capacidades CMM , montaxe, embalaxe e entrega.
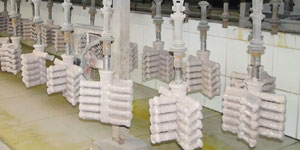
Certificado ITAF16949. Inclúe servizo de fundición adicional fundición de investimento,fundición de area,Fundición por gravidade, Fundición de escuma perdida,Fundición centrífuga,Fundición ao baleiro,Fundición permanente de moldesAs capacidades inclúen EDI, asistencia en enxeñaría, modelado sólido e procesamento secundario.
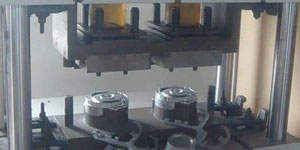
Industrias de fundición Estudos de casos de pezas para: coches, bicicletas, avións, instrumentos musicais, motos acuáticas, dispositivos ópticos, sensores, modelos, dispositivos electrónicos, caixas, reloxos, maquinaria, motores, mobles, xoias, discos, telecomunicacións, iluminación, dispositivos médicos, dispositivos fotográficos, Robots, esculturas, equipos de son, equipos deportivos, ferramentas, xoguetes e moito máis.
Que podemos axudarche a facer a continuación?
∇ Ir á páxina de inicio para China Fundición a Presión
→Pezas de fundición-Descubre o que fixemos.
→ Consellos recomendados sobre Servizos de fundición a presión
By Fabricante de fundición a presión Minghe | Categorías: Artigos útiles |material tags: Fundición de aluminio, Fundición de cinc, Fundición de magnesio, Fundición de titanio, Fundición de aceiro inoxidable, Fundición de latón,Fundición de bronce,Emisión de vídeo,Historia da empresa,Fundición en aluminio | Comentarios desactivados