O control de procesos da produción de ferro vermicular
En comparación co ferro gris, a resistencia á tracción do ferro vermicular aumenta polo menos nun 70%, o módulo de elasticidade aumenta un 35% e a resistencia á fatiga case duplícase. En comparación coa aliaxe de aluminio, a resistencia e rixidez do ferro vermicular son dúas veces maiores e a resistencia á fatiga é dúas veces maior. Estas características do ferro vermicular proporcionan ao motor a posibilidade de mellorar a relación potencia / peso e aumentar a presión do cilindro. O aumento da presión dos cilindros é a clave para un rendemento óptimo do motor diésel de inxección directa de nova xeración. Para satisfacer a aplicación xeneralizada de ferro vermicular, a industria de fundición está a prepararse activamente, investindo intensamente e reconstruíndo novos procesos para facer estable e fiable a produción de ferro vermicular.
Para os motores de ferro vermicular desde o prototipo ata a produción en serie, o factor decisivo é o risco de calidade. Para o ferro vermicular de alta calidade, a zona estable é moi pequena, só no rango do 0.008% de contido de magnesio. Unha cantidade de traza, como unha perda do 0.001% de magnesio, producirá grafito en escamas, o que fará que as propiedades mecánicas caian entre un 25% e un 40%. Este artigo describe un sistema de control de procesos baseado en métodos de análise térmica. O sistema mide a perda de magnesio e axusta o estado do ferro fundido en liña para evitar a xeración de grafito en escamas. Este método de medición e axuste de control en liña reduce a volatilidade no proceso de produción de ferro vermicular ata o punto máis baixo e elimina fundamentalmente o risco de calidade causado pola produción de ferro vermicular.
A demanda de alta potencia, par elevado, baixas emisións de escape e reducido consumo de combustible segue crecendo. Isto obriga aos deseñadores de motores diésel de alta potencia a aumentar a presión máxima de ignición, o que aumenta moito a carga térmica e a carga mecánica do motor. A carga térmica e a carga mecánica aumentan ao mesmo tempo, de xeito que os motores convencionais de fundición e aliaxe (CrMo) que se utilizan actualmente alcanzaron ou superaron o límite superior do seu uso. Os fabricantes de motores necesitan materiais con maior resistencia e mellor resistencia á calor.
O ferro vermicular converteuse rapidamente no material escollido para as persoas. Mellora moito a fiabilidade do bloque de cilindros, a culata e o forro da nova xeración de motores de camións. Para conseguir a mellor combinación de varias propiedades (como propiedades de fundición, propiedades de mecanizado, condutividade térmica e propiedades mecánicas), estas pezas deben realizarse cunha taxa de esferoidización do 0% ao 20% (taxa de arrastre do 80% ao 100% ) Feita de ferro vermicular. Se a taxa de esferoidización supera o 20%, causará unha serie de factores desfavorables. Por exemplo, a cantidade de contracción é demasiado grande e as pezas con formas complexas como as culatas son especialmente propensas á contracción. Outro exemplo é a redución da vida útil da ferramenta debido ao desgaste excesivo durante o mecanizado. Tamén hai unha diminución significativa da condutividade térmica, provocando tensións térmicas, etc. No outro extremo do ferro vermicular, a aparición de grafito en escamas provocará un descenso lineal das propiedades mecánicas, facendo que o motor non poida cumprir os novos requisitos. En resumo, para satisfacer as necesidades da nova xeración de motores de camións, a taxa de esferoidización do ferro vermicular de alta resistencia debe estar comprendida entre o 0% e o 20% (é dicir, a taxa de rastrexo é superior ao 80%, sen folerpas).
Se se usa ou non o control do proceso de produción depende da produción anual do produto, da complexidade do produto e da gama permitida de cambios na estrutura metalográfica. Como se mostra na figura 1, as pezas relativamente sinxelas e de baixo volume, como os lingotes, xeralmente pódense producir mediante métodos de fundición convencionais. O control de procesos xeralmente non é necesario e non é economicamente rendible. Cando a produción anual de compoñentes aumenta, como tubos de escape, manguitos e soportes, debería ter sentido introducir o control do proceso. Aínda que este tipo de produto ten unha gran produción anual, a tonelaxe anual de fundición non é elevada. Os requirimentos da estrutura metalográfica non son moi estritos, o que permite que a taxa de esferoidización sexa do 50%. Ademais, debido á pouca cantidade de mecanizado destas pezas, pódese permitir que o aumento de titanio que se pode engadir na produción amplíe o rango controlable. Para este tipo de produtos, os métodos de fundición convencionais e un rigoroso adestramento son xeralmente competentes para a produción de ferro vermicular. Pero desde a perspectiva do control de calidade, o control de procesos debería ser máis seguro. Do mesmo xeito, o control de procesos tamén ofrece unha garantía para a produción de grandes bloques de motores mariños e culatas. Aínda que o gran tamaño e a baixa cantidade de produción son propicios para a fabricación de produtos, as perdas económicas causadas polos produtos que superan o estándar son suficientes para engadir un conxunto de sistema de control de procesos.
Os produtos que máis necesitan control de proceso son bloques de cilindros de motores de automóbiles, culatas e discos de freo con gran produción anual, alta complexidade e rigorosos requisitos técnicos. O volume de produción anual e a tonelaxe anual destes produtos son moi elevados. Son de tamaño complexo, esixentes na estrutura metalográfica e tenden a producir cavidades de contracción. Estes produtos non deben ter riscos de calidade, se non, a perda será moi grave.
Os estritos requisitos sobre o rendemento do bloque do motor, a culata e o asento do cilindro sentaron as bases para a fabricación das especificacións do produto. Para obter o mellor rendemento integral de moldabilidade, mecanización e propiedades mecánicas, a taxa de esferoidización debería estar comprendida entre o 0% e o 20% en todas as partes clave do compoñente. O que é máis importante, o grafito en escamas debe evitarse absolutamente para evitar danos nas pezas causados pola debilidade local. Para conseguir unha boa aditividade mecánica, os carburos libres deben reducirse ao mínimo. Polo tanto, nunca se debe engadir titanio. Finalmente, desde o punto de vista da produción, a fundición precisa un proceso estable e fiable para garantir a menor taxa de chatarra causada pola estrutura metalográfica. Os fabricantes da industria do automóbil requiren unha garantía de calidade e o 100% das pezas fundidas deben cumprir os requisitos metalográficos. A produción a gran escala e fiable de bloques de cilindros, culatas e asentos de cilindros require unha análise precisa e un axuste en liña do ferro fundido para eliminar as flutuacións do proceso antes de verter.
Estabilidade vermicular do ferro
A razón pola que o ferro compactado non se usa en grandes cantidades para producir pezas complexas (como bloques de motores) débese a que a área estable do ferro compactado é demasiado pequena para garantir que non haxa risco na produción. En xeral, esta zona estable só abarca a área do 0.008% de magnesio, como se mostra na figura 2. O tamaño e a posición da plataforma na zona estable varían segundo o produto. De feito, a gama de magnesio dispoñible é menor que esta. Porque cada 5 minutos, o magnesio activo queimará un 0.001%. O punto inicial de vertido do ferro fundido debe estar suficientemente afastado do punto de xiro pronunciado do ferro compactado ao ferro gris para garantir que non apareza grafito en escamas na parte fundida final. Cando se engade magnesio ao ferro fundido, o grafito en escamas aparecerá nuns 15 minutos.
O punto de partida non debe estar moi preto do lado dereito da plataforma estable (alto contido en magnesio), se non, fará que se forme unha gran cantidade de grafito esferoidal na parte máis delgada e na parte de arrefriamento rápido.
Ademais da pequena área de plataforma dispoñible, a área de plataforma sempre está en movemento. Se o contido de osíxeno activo e xofre é alto, consumirán máis magnesio activo e toda a plataforma desprazarase cara á dereita (alto contido en magnesio). Pola contra, se o contido de osíxeno activo e xofre é baixo, a plataforma moverase cara á esquerda (baixo contido de magnesio). Os cambios na composición das materias primas, a pureza, o grao de oxidación e humidade, etc., imposibilitan ás persoas controlar o ferro vermicular cun rango fixo de composición química.
Aínda que a conversión de ferro vermicular a ferro gris só precisa reducir o magnesio activo nun 0.001%, a queima de magnesio non provoca que toda a parte se converta en grafito en escamas. Cando o magnesio activo non é suficiente, o grafito primeiro forma folerpas e expándese cara a fóra a medida que se solidifica e o magnesio cae e concéntrase no extremo frontal da interface sólido-líquido. Se a cantidade inicial de magnesio activo é axeitada, formarase grafito vermicular no límite do eutéctico, como se mostra na Figura 3. O grafito en escamas aparece por primeira vez como manchas de grafito en escamas dispersas. A diferenza de todos os grafitos en escamas comúns, estas manchas illadas de grafito en escamas son difíciles de detectar mediante ultrasóns. A probabilidade de que sexan escaneadas por ultrasóns non é alta.
A sensibilidade do magnesio ao ferro vermicular pódese mostrar na Figura 4: Nunha tonelada de cucharón de metal quente, só hai que engadir 10 gramos de magnesio, as manchas de grafito en escamas dispersas na mostra de proba Φ25 pódense transformar completamente en grafito vermicular. A resistencia á tracción da barra de proba con manchas de grafito en escamas é de só 300 MPa, mentres que a resistencia á tracción da mesma barra de proba con fluencia completa alcanza os 450 MPa.
O inoculante tamén é moi sensible á plataforma estable de ferro vermicular, como se mostra na figura 5: engadir 80 gramos de inoculante a unha tonelada de ferro fundido aumentará a taxa de esferoidización na barra de proba Φ25 do 3% ao 21%. A cantidade de inoculación é elevada e o núcleo cristalino é numeroso, o que é propicio para a formación de grafito esférico. Isto eleva a plataforma de ferro vermicular na dirección de alta velocidade de esferoidización. A baixa taxa de inoculación fai que a plataforma desprácese cara a abaixo. Numerosos factores, como a temperatura de sobrecalentamento do ferro fundido, o tempo de retención, a composición química das materias primas, o tipo de inoculante e a cantidade de inoculación, afectarán á posición da plataforma de ferro vermicular.
O requisito máis básico de calquera tecnoloxía de control de procesos é medir e analizar con precisión o estado do ferro fundido. Para o ferro vermicular, un control de produción fiable require a medición simultánea do punto crítico do magnesio activo a partir da transición de fluencia-cinza, o grao de queimadura de magnesio posterior e o grao de inoculación.
A mostra de análise térmica de 200 gramos obtense inserindo a sonda Xinte no ferro fundido despois da esferoidización e a inoculación. Durante o proceso de inserción de tres segundos, a parede da sonda e o ferro fundido alcanzan un estado de equilibrio térmico. Diferente do vaso de mostra de análise térmico convencional, este mostraxe de paredes delgadas non só garante o mesmo volume de mostra cada vez, senón que tamén evita a oxidación do ferro fundido que se verte no vaso de mostra. A medición do superquecemento é máis precisa porque non hai fenómeno como o fenómeno da condensación violenta na análise térmica convencional.
Como se mostra na Figura 6a, a sonda Xinte está feita de chapa de aceiro estirada prensada. Basicamente é un recipiente esférico. A delgada parede de aceiro que contén o ferro fundido ten unha capa de illamento parecida a un matraz. O espesor da capa de illamento está engrosado simétricamente segundo a dirección da altura para garantir unha disipación e arrefriamento uniformes da calor ao contorno, e a auga de ferro zz nela está próxima á solidificación dun corpo esférico. No tubo de protección da sonda hai dúas termopares de tipo N. O termopar pode extraerse despois de cada medición e usarse repetidamente máis de 100 veces. Un dos dous termopar está situado na parte inferior do recipiente e o outro está no centro térmico do recipiente. Dado que o recipiente é esférico e está suspendido libremente (isto é diferente do vaso de mostra de análise térmico convencional que descansa sobre un soporte que absorbe o calor), o ferro fundido xera un fluxo de calor uniforme no recipiente, como se mostra na figura 6b. Este fluxo de calor fai que o ferro fundido se trate continuamente no recipiente, formando unha partición de fluxo na parte inferior da sonda.
Para imitar a perda natural de ferro fundido durante a vertedura, hai un revestimento na parede da sonda que reacciona co magnesio activo. O ferro fundido flúe ao longo da parede revestida impulsado polo fluxo de calor. Despois da reacción, o contido de magnesio do ferro fundido diminúe e acumúlase no compartimento da parte inferior do recipiente. Falando directamente: o termopar no centro da sonda mide o ferro fundido sen reaccionar, que é o estado inicial de vertedura; o termopar na parte inferior mide o estado despois do remate. A formulación do revestimento reactivo é moi particular. Debe asegurarse con precisión de que o ferro fundido acumulado no compartimento é un 0.003% menos activo que o ferro fundido central. Polo tanto, se o contido inicial de magnesio está moi preto do punto de inflexión da cinza rastreira, o ferro fundido no compartimento xerará ferro gris, que será medido polo termopar nesta zona. Deste xeito, ao comezo do lanzamento, o taller pode engadir máis magnesio para compensar a inevitable perda de queima de magnesio.
Se o termopar na parte inferior mostra unha curva de ferro vermicular, indica que o contido inicial de magnesio é o suficientemente alto como para que non haxa grafito en escamas despois do final do lanzamento.
A Figura 7 é un diagrama de erosión en sección transversal da sonda Xinte despois da medición da mostra. Na figura pódese ver claramente a área de partición, a área de mostra principal e o tubo de protección do termopar. Como o magnesio activo redúcese nun 0.003%, fórmanse matrices de grafito e ferrita en forma de D na zona de separación. O tamaño da área de grafito en escamas na parte inferior reflicte directamente o contido inicial de magnesio na área de mostra principal. O tamaño desta zona pódese calcular a partir da calor liberada na parte inferior. O coeficiente de regresión de varianza entre a liberación de calor e o tamaño da partición supera 0.9, o que demostra que a relación entre ambas é moi estreita. A calor liberada obtense pola integración temporal da curva de arrefriamento. Este método de medición do estado do ferro fundido na corrente e ao final da vertedura garante á vez a precisión do contido de magnesio antes da vertedura.
Dado que o ferro vermicular é moi sensible aos axentes esferoidantes e inoculantes, é imposible que as fundicións empreguen os métodos de tratamento excesivos empregados na produción de ferro gris e dúctil. Como se mostra na Figura 8, debido á súa sensibilidade, o ferro vermicular só é estable dentro dunha fiestra cadrada, non só na área da plataforma de magnesio. Un proceso fiable de produción de ferro vermicular debe controlar a esferoidización e a inoculación de principio a fin para garantir que a estrutura metalográfica cumpre o obxectivo.
Por moito esforzo que se faga, por estrita que sexa a xestión, a flutuación do ferro fundido sempre é inevitable. Non digamos o preciso que a xente sabe sobre o tratamento do ferro fundido, os métodos de tratamento dun só paso, como o método sandwich, non poden garantir que cada tratamento caia dentro da estreita fiestra vermicular de ferro. Numerosas variables de produción, como a relación de mestura, a temperatura do forno, o tempo de suxeición, o grao de precalentamento do cucharón de ferro fundido, a velocidade de golpeo, a posición de golpeo do ferro fundido (medida dentro ou fóra), o peso do ferro fundido, o estado da bolsa de aliaxe, o axente esferoidante. o contido real de magnesio de (PeSiMg), a disposición de aliaxes de cada capa no método sandwich e a cobertura de limas de chatarra, etc., afectarán á absorción de magnesio. Ademais destes factores, o contido de osíxeno activo e xofre activo tamén cambiará o tamaño e a posición da ventá de ferro vermicular. Os cambios no tempo de residencia do ferro fundido no cucharón, o tempo de transporte e o tempo de vertido cambiarán o tempo de queima dispoñible.
Non obstante, os factores de flutuación máis imprevisibles son os erros do operador ou as diferenzas entre os distintos operadores debido a diferentes hábitos de traballo.
Na produción en masa a gran escala, o único xeito seguro é medir as características de solidificación do ferro fundido despois do tratamento. Deste xeito, varios factores que afectan o tamaño, a posición e a absorción de aliaxes da ventá de ferro vermicular medíronse, analizáronse e consideráronse de forma completa. Despois pódese engadir a cantidade adecuada de magnesio e inoculante. Cada cucharón de ferro fundido vértese despois de actualizalo a un estado ideal. Este método de control do proceso de medición e axuste en dous pasos minimiza a variabilidade da produción e elimina por completo o risco de grafito en escamas na fundición.
Control de procesos de produción de ferro vermicular con cucharón de metal quente
Como se mostra na Figura 9, o control do proceso comeza coa análise térmica do ferro fundido despois do tratamento inicial de esferoidización e inoculación. Segundo o resultado da análise, a máquina de alimentación de fíos mostra automaticamente a lonxitude do fío que se engadirá con magnesio e inoculante e agarda que o operador o inicie. Cando se completa a liña de alimentación, o cucharón envíase inmediatamente á liña de fundición. Todo o proceso de medición e axuste leva uns tres minutos. Durante este período, o taller pode realizar tratamentos convencionais de pre-fundición, como a eliminación de escorias. Isto garante a continuidade da liña de fundición.
Desde o punto de vista operativo, o ferro fundido en bruto non contén magnesio e a súa capacidade de incubación tamén é moi limitada. Despois da esferoidización e inoculación, o magnesio e os inoculantes comen primeiro o osíxeno activo e o xofre do ferro fundido e despois "saltan" o ferro fundido a unha determinada posición no taboleiro. No exemplo da Figura 10, o índice de magnesio e o índice de inoculación do ferro fundido son 65 e 45, respectivamente. Debido a que os principais parámetros de cambio da produción de sombra móstranse no ferro fundido despois da medición e tratamento, os resultados da análise térmica reflicten directamente o estado actual do ferro fundido. Só queda engadir a cantidade adecuada de magnesio e inoculante para elevar o ferro fundido desde a súa posición actual ata o punto de partida requirido. No exemplo da figura 10, engádense primeiro sete unidades de cables de magnesio e despois engádense 23 unidades de cables inoculantes. A relación correspondente entre a unidade de índice e a lonxitude do cable está calibrada segundo o produto e o taller e compílase no programa. Baseado na experiencia pasada de case 100,000 pezas fundidas de ferro vermicular, a cantidade media de cable de magnesio engadida é de 5 metros por tonelada. Contén 12 gramos de magnesio por metro e calculada a unha taxa de absorción do 50%, a cantidade de magnesio engadida por tonelada de ferro fundido é de só 30 gramos. Dado que a cantidade de adición é moi pequena e os principais cambios xa se produciron no tratamento inicial, o axuste é moi eficaz e fiable. Despois do axuste, non fai falta facer análises térmicas.
No tratamento inicial, o estado posterior ao tratamento debe ser inferior á posición inicial de vertedura, de xeito que, aínda que todos os factores que son beneficiosos para a absorción de magnesio e inoculante alcanzan o valor óptimo, o ferro fundido só alcanzará o estado de vertido inicial . Excepto para non tratar en exceso, o ferro fundido despois do tratamento non está no estado de ferro gris e ferro branco. Para facer o proceso de fundición máis eficiente, o índice de magnesio e o índice de inoculación de cada cucharón de ferro fundido móstranse no diagrama de bloques do proceso. Segundo a tendencia cambiante do diagrama de bloques, o operador pode axustar a cantidade de ferro fundido engadida ao seguinte cucharón. O valor equivalente de carbono tamén se mostra na pantalla. Estes datos editáronse e almacenáronse no rexistro de produción, de xeito que se poden rastrexar e completar e tamén cumpren os requisitos de garantía de calidade.
Aínda que a análise térmica e os axustes posteriores poden asegurar a produción de ferro vermicular, recoméndase que se tomen mostras da copa do colado final para a súa análise. En comparación coa inspección de calidade convencional, este resultado da análise térmica pode proporcionar análise en liña e clasificar as pezas fundidas se fose necesario. A simulación da perda de magnesio na sonda fai que esta técnica de inspección "non destrutiva" sexa máis eficaz que os métodos metalográficos e ultrasóns. Debido a que este método mide un tamaño de mostra maior, tamén detecta como se solidificará o ferro fundido nos próximos 10-15 minutos.
Para resumir
A elección do sistema de control do proceso depende do produto e do proceso de fundición. Ao lanzar produtos complexos como a tapa do motor de ferro vermicular e o cilindro, o sistema debe controlar simultaneamente o contido de magnesio e inoculante para que quede nunha xanela moi estreita desde o principio ata o final da vertedura. A taxa de esferoidización debe estar comprendida entre o 0% e o 20% (taxa de arrastre entre o 80% e o 100%) para garantir a mellor moldabilidade, aditividade mecánica e outras prestacións completas e a mellor función de uso. As manchas de grafito en escamas deben eliminarse completamente para evitar defectos e debilidades locais.
O punto de partida de calquera sistema de control de procesos é medir con precisión e eficacia o estado do ferro fundido. A produción fiable de ferro vermicular a gran escala debe ter métodos de control factibles para eliminar os cambios no proceso e os erros de funcionamento do ser humano. O xeito máis eficaz de eliminar os cambios no proceso é realizar unha análise térmica sobre o ferro fundido despois da esferoidización e a inoculación. Segundo os resultados da análise térmica, engádese unha cantidade precisa de magnesio e inoculante antes de verter. Este método de axuste e medición en liña garante a estabilidade da liña de produción de fundición e elimina varios riscos derivados da produción de ferro vermicular a gran escala.
Mantén a fonte e o enderezo deste artigo para reimprimilos: O control de procesos da produción de ferro vermicular
Minghe Compañía de Fundición a Presión dedícanse á fabricación e proporcionan pezas de fundición de calidade e alto rendemento (a gama de pezas de fundición a presión de metal inclúe principalmente Fundición a presión de parede delgada,Fundición a cámara quente,Fundición a cámara fría), Servizo redondo (servizo de fundición a presión,Cnc mecanizado,Fabricación de moldes, Tratamento de superficie). Calquera requirimento de fundición a presión de aluminio, magnesio ou fundición de Zamak / cinc e outros requisitos de fundición son benvidos para poñerse en contacto connosco.
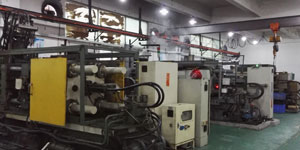
Baixo o control de ISO9001 e TS 16949, todos os procesos lévanse a cabo a través de centos de máquinas de fundición a presión avanzadas, máquinas de 5 eixes e outras instalacións, que van dende as blasters ata as lavadoras Ultra Sonic. Minghe non só ten equipos avanzados senón que tamén ten profesionais equipo de enxeñeiros, operadores e inspectores experimentados para facer realidade o deseño do cliente.
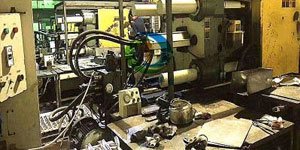
Fabricante por contrato de pezas fundidas. As capacidades inclúen pezas de fundición de aluminio a cámara fría de 0.15 libras. ata 6 libras, configuración rápida de cambio e mecanizado. Os servizos de valor engadido inclúen o pulido, vibración, desbarbado, granallado, pintura, revestimento, revestimento, montaxe e ferramentas. Entre os materiais traballados inclúense aliaxes como 360, 380, 383 e 413.
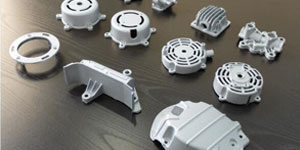
Servizos de enxeñaría simultánea de asistencia ao deseño de fundición por cinc. Fabricante a medida de pezas de fundición de cinc de precisión. Pódense fabricar pezas fundidas en miniatura, pezas fundidas de alta presión, pezas de molde de varias diapositivas, pezas de molde convencionais, pezas de moldaxe de pezas individuais e pezas de fundición independentes e pezas de fundición seladas. As pezas fundidas pódense fabricar en lonxitudes e anchuras de ata 24/0.0005 polgadas +/- XNUMX polgadas de tolerancia.
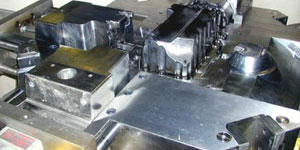
Fabricante certificado ISO 9001: 2015 de magnesio fundido a presión, as capacidades inclúen fundición a presión de magnesio de alta presión ata cámara quente de 200 toneladas e cámara fría de 3000 toneladas, deseño de ferramentas, pulido, moldeado, mecanizado, pintura en po e líquido, QA completo con capacidades CMM , montaxe, embalaxe e entrega.
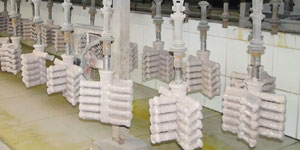
Certificado ITAF16949. Inclúe servizo de fundición adicional fundición de investimento,fundición de area,Fundición por gravidade, Fundición de escuma perdida,Fundición centrífuga,Fundición ao baleiro,Fundición permanente de moldesAs capacidades inclúen EDI, asistencia en enxeñaría, modelado sólido e procesamento secundario.
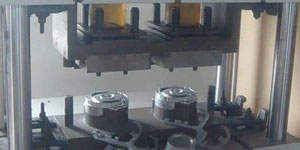
Industrias de fundición Estudos de casos de pezas para: coches, bicicletas, avións, instrumentos musicais, motos acuáticas, dispositivos ópticos, sensores, modelos, dispositivos electrónicos, caixas, reloxos, maquinaria, motores, mobles, xoias, discos, telecomunicacións, iluminación, dispositivos médicos, dispositivos fotográficos, Robots, esculturas, equipos de son, equipos deportivos, ferramentas, xoguetes e moito máis.
Que podemos axudarche a facer a continuación?
∇ Ir á páxina de inicio para China Fundición a Presión
→Pezas de fundición-Descubre o que fixemos.
→ Consellos recomendados sobre Servizos de fundición a presión
By Fabricante de fundición a presión Minghe | Categorías: Artigos útiles |material tags: Fundición de aluminio, Fundición de cinc, Fundición de magnesio, Fundición de titanio, Fundición de aceiro inoxidable, Fundición de latón,Fundición de bronce,Emisión de vídeo,Historia da empresa,Fundición en aluminio | Comentarios desactivados