O proceso de produción do tambor de freo para camión
O tambor de freo é unha parte de seguridade, está relacionado coa seguridade da vida e da propiedade humana e, ao mesmo tempo, é unha parte vulnerable e consumible. A demanda do mercado é particularmente grande.
Na actualidade, a produción anual nacional é de aproximadamente 10 millóns ou máis. Debido a que a estrutura do produto é relativamente sinxela, o modelado manual e manual son fáciles de usar e hai fundicións que producen tambores de freo en case todas as partes do país. Varias grandes empresas que visitei producen tambores de freo nunha liña de montaxe mecanizada, cunha produción anual de aproximadamente un millón.
Tamén estiven en algunhas pequenas empresas cunha produción anual de decenas de miles. Tamén hai un parque industrial nunha cidade do condado de Longyao, Hebei, onde máis de cen fundicións están producindo intensamente tambores de freo para automóbiles; a produción de tambores de freo en todo o distrito debería ser superior a un millón. É só que os bidóns de freo producidos por grandes empresas son generalmente subministrados a fábricas de eixes nacionais ou exportados ao exterior, mentres que a maioría dos bidóns de freo producidos por pequenas empresas son subministrados ao mercado de pezas e post-venda. A súa calidade de produto e credibilidade son difíciles de aceptar polas fábricas de eixos habituais. Segundo estas empresas, vin e aprendín, debido ás diferentes estruturas do produto e aos obxectivos de subministración diferentes, os procesos de produción son diferentes, pero en xeral, o problema de calidade Aínda hai moitos que non cumpren os requisitos de calidade dos tambores de freo automotivos. Por iso, creo que é necesario discutir e investigar o proceso de produción de tambores de freo con vostede e intercambiar experiencia entre si. O seguinte baséase na miña experiencia e comprensión. Situación, aproveite esta oportunidade para intercambiar opinións contigo, corrígame se está mal.
Requisitos de calidade para bidóns de freo de camión
Debido a que a fundición gris ten unha boa condutividade térmica, absorción de choque, resistencia ao desgaste, excelente rendemento de fundición e baixo custo de fabricación, case todos os tambores de freo dos vehículos de motor están feitos de fundición gris e os graos son HT200 e HT250.
Só hai un estándar de fundición gris no meu país que é JB / T9439-2010 e non hai un estándar especial de fundición gris para os tambores de freo de automóbil. No estándar da máquina non hai ningunha descrición de fundición gris especial. No mundo, só a Sociedade Americana de Ensaios e Materiais ASTMA159-83 (reexaminada en 1993) formulou normas especialmente para as pezas de ferro gris para automóbiles. Hai 3 graos de ferro fundido listados para o tambor de freo segundo a súa capacidade de carga. Ao mesmo tempo, os requisitos de calidade para tambores de freo no estándar de fundición gris para maquinaria eléctrica da American Society of Automotive Engineers SAEJ431 son basicamente os mesmos que ASTMA159-83. Na actualidade, a maioría do noso país e de países estranxeiros refírense ás normas estadounidenses sobre tambores de freo. O estándar de fábrica aparece no estándar de debuxo ou aceptación. O nivel dun estándar reflicte o seu nivel de artesanía e calidade. Só os estándares de alto nivel poden producir produtos de alta calidade.
O seguinte introduce brevemente os estándares americanos mencionados e os requisitos de calidade dalgunhas boas empresas estranxeiras en tambores de freo, e introduce o seguinte como referencia
As propiedades mecánicas
Grao | Resistencia á tracción (MPa) | Dureza (HB) |
G2500a |
175 |
170-229 |
G3500b |
245 |
207-255 |
G3500c |
245 |
207-255 |
composición química
Grao | C total |
Si |
Mn |
P |
s |
Outros elementos de aliaxe |
G2500a |
≥ 3.40 |
1.60-2.10 |
0.60-0.90 |
≤ 0.15 |
≤ 0.12 |
Como é necesario |
G3500b |
≥ 3.40 |
1.30-1.80 |
0.60-0.90 |
≤ 0.15 |
≤ 0.12 |
|
G3500c |
≥ 3.50 |
1.30-1.80 |
0.60-0.90 |
≤ 0.15 |
≤ 0.12 |
Nota:
- O C total é un requisito obrigatorio e debe estar garantido
- Outros elementos como Cr, Cu, Sn úsanse principalmente para garantir propiedades mecánicas e dureza.
- G2500a úsase en camións de servizo medio, G3500b úsase en camións de servizo pesado e G3500c úsase en camións de carga pesada.
Microestrutura
Grao | Tipo de grafito | Shi Chang | Hipokeimenon |
G2500a |
A |
2-4 |
Perlita lamelar, ferrita <15% |
G3500b |
A |
3-5 |
Perlita en capas, ferrita + cementita <5% |
G3500c |
A |
3-5 |
Perlita en capas, ferrita + cementita <5% |
Outros requisitos
Ademais da aceptación de propiedades mecánicas, dureza e metalografía, os fabricantes estranxeiros e os OEM nacionais adoitan presentar requisitos de compacidade nas condicións técnicas dos tambores de freo proporcionados.
Se hai buratos de contracción, porosidade de contracción, poros, inclusións de area ou outros defectos de fundición nas pezas fundidas, non serán densos. Estes defectos pódense comprobar mediante raios X ou métodos anatómicos. Se os defectos son inferiores aos especificados na seguinte táboa, pódese aceptar. O exceso do seu regulamento xulgarase como chatarra. Por suposto, se o defecto foi exposto durante o mecanizado, xeralmente non se acepta.
- ASTME446-98 A calidade interna do tambor de freo é o nivel de defectos probado en X.
- Área densa avanzada, a cualificación é A3, B3, C2
- Área xeralmente densa, o nivel de recepción é A3, B4, C3
- Nota: A significa estomas, A3 significa que o nivel de aceptación dos estomas é 3
- B representa area e inclusións B4 representa o nivel de aceptación das inclusións de area é nivel 4
- C significa porosidade de contracción C3 significa que o nivel de aceptación de porosidade de contracción é 3
Modos de avaría e causas dos tambores de freo
A falla do tambor de freo durante o uso é principalmente craqueamento e abrasión, pero a partir das estatísticas de datos reflectidas nas reclamacións e reclamacións dos clientes, é principalmente a primeira. É dicir, a maioría dos tambores de freo fallados están baixo un desgaste normal ou incluso leve, é dicir, racháronse e non se poden usar. A continuación móstranse os restos devoltos por unha fábrica en 2014. Na imaxe pódese ver claramente que se xeran unha ou varias fendas lonxitudinais no tambor do freo. As fendas transversais aparecen principalmente nas esquinas redondeadas da brida, normalmente coñecidas como caída superior.
Da análise do fallo das partes falladas, conclúese que hai tres razóns principais para o fallo:
- As propiedades mecánicas do corpo de fundición son inferiores aos requiridos normais
- Hai defectos de fundición dentro da fundición, especialmente a porosidade de contracción nas esquinas redondeadas da brida.
- O coche está sobrecargado, frea con frecuencia e pulverízase con auga durante o proceso de freada, e as propiedades mecánicas e a metalografía desas pezas falladas compróbanse para cumprir os requisitos do produto.
As dúas primeiras causas do fallo deberían ser melloradas por aqueles que producimos tambores de freo. Estabilizar e mellorar a calidade do tambor de freo. Debaterei contigo con máis detalle a continuación. En canto á terceira razón do fracaso, somos impotentes, dependendo principalmente da gobernanza estatal do uso ilegal de vehículos con sobrecarga. Dende o punto de vista das reclamacións, unha gran parte dela é causada por ese uso ilegal. Non obstante, a responsabilidade transfírese xeralmente á fundición. Polo que sei, varias empresas que producen tambores de freo reclamaron unha proporción de reclamacións de aproximadamente o 3%. Hai millóns de compensacións cada ano. De feito, este tipo de responsabilidade debe ser asumida polo propietario do coche. Os tambores de freo exportados do noso país a países estranxeiros xeralmente reflicten ben. Case nunca hai indemnización nin sequera denuncias. Os tambores de freo dos turismos e os coches transportados en zonas planas tamén reflicten ben. Só unhas poucas zonas montañosas, áreas mineiras e produtos individuais teñen unha vida útil baixa, todo isto causado por unha sobrecarga doméstica grave, freos frecuentes de emerxencia e pulverización de auga para arrefriar o tambor de freo durante o proceso de freada. Neste caso, toda a enerxía cinética convértese na carga térmica do tambor de freo, que se pode medir ata 800 ℃ -850 ℃. Isto tamén se pode atopar a partir do exame macroscópico e metalográfico da fenda de falla. Este tipo de fundición é macroscópicamente branca e brillante. Metalograficamente, é grafito + martensita + bainita. Estes son producidos por temperado de austenita despois da transformación a alta temperatura. Polo tanto, o tambor do freo falla baixo a acción da tensión de flexión, a tensión térmica e a resistencia á forza de freada mecánica en vez de ao craqueo convencional. Este pode ser un modo de fallo ao estilo chinés.
1. Proceso de produción do tambor de freo
O proceso de produción de tambores de freo céntrase principalmente en dous aspectos. Unha delas é como garantir as súas propiedades mecánicas e a súa estrutura metalográfica para cumprir os requisitos do produto. Pero como reducir os seus defectos de fundición. Especialmente os defectos internos das pezas clave. En termos de redución de defectos de fundición, hoxe voume centrar en como reducir os seus defectos de contracción, porque é o principal tipo de residuos e un dos principais motivos do fallo.
O primeiro aspecto é principalmente proporcionar unha mellor calidade metalúrxica do ferro fundido. O segundo aspecto é descubrir os medios tecnolóxicos adecuados para o fabricante.
Na actualidade, os materiais dos bidóns domésticos de freo de camión son HT250, polo que vou centrarme en varias cuestións ás que hai que prestar atención na fundición e no proceso de HT250 empregado na produción de bidóns de freo.
Orixinalmente, se só necesitásemos cumprir as propiedades mecánicas de HT250 e os requisitos de estrutura metalográfica, non habería dificultade. Non obstante, o HT250 utilizado nos tambores de freo debe garantir propiedades mecánicas, dureza e estrutura metalográfica baixo un alto contido de carbono, o que supón algunhas dificultades para algúns pequenos e incluso algúns grandes fabricantes. Propuxeron que se o contido de carbono do produto é superior ao 3.40%, sen engadir Cr, Cu, Sn e outros elementos de aliaxe, é difícil garantir o rendemento. Pero a súa realidade é aforrar custos e, en xeral, só engaden Cr e Sn para garantir a perlita e a resistencia á tracción. Non obstante, se a cantidade engadida é pequena, non se alcanzará a resistencia e dureza e, se a cantidade engadida é grande, haberá unha cantidade excesiva de cementita na metalografía.
E nun dilema. Finalmente, para medir os pros e os contras, a maioría deles adopta o método de redución do contido de carbono para cumprir os requisitos de propiedades mecánicas e dureza. Por suposto, ata o momento, aínda que a norma ASTM estableceu regulacións estritas sobre o contido en C, as fábricas chinesas non a implementaron. Incluso algúns clientes estranxeiros non requiriron uniformemente que o contido de carbono sexa superior ao 3.4% ou superior. Por exemplo, moitos clientes que coñezo, os seus requisitos para a composición química dos tambores de freo son os seguintes:
Nome do cliente |
C |
Si |
Mn |
P |
s |
Cr |
Cu |
Sn |
TurquíaADR Ltd. |
3.2-3.4 |
2.0-2.4 |
0.7-1.0 |
≤ 0.2 |
≤ 0.1 |
0.15-0.4 |
0.15-0.5 |
≤ 0.12 |
Hyundai 250D |
3.1-3.8 |
1.5-2.5 |
0.4-0.9 |
≤ 0.2 |
≤ 0.1 |
0.15-0.4 |
0.15-0.5 |
≤ 0.12 |
Non obstante, o aumento do contido total de carbono baséase cientificamente e é a tendencia xeral, porque só un alto contido en carbono pode garantir unha gran cantidade de grafito e ter unha mellor condutividade térmica e resistencia á fatiga térmica. A normativa obrigatoria feita polos Estados Unidos debe ter a súa base científica. Para nós, tamén debemos ter a capacidade de producir propiedades mecánicas cualificadas, dureza e estrutura metalográfica baixo a premisa dun alto contido en carbono.
A través da práctica doméstica de producir ferro fundido de alta resistencia con alto contido de carbono ao longo dos anos, débese dicir que se acumulou moita experiencia exitosa e que se logrou un consenso en tecnoloxía. Isto sentou unha boa base para a nosa produción de tambores de freo e a situación real tamén é certa. A calidade dos tambores de freo producidos por moitas grandes empresas foi capaz de satisfacer as necesidades dos clientes de forma estable. Estas tecnoloxías, en resumo, están tomando o camiño do ferro fundido sintético. A tecnoloxía adoptada baséase na elevada proporción de chatarra de aceiro engadida, utilizando un recarburador para aumentar a recarburación, aumentar o xofre no ferro fundido, unha boa incubación e un ferro fundido suficientemente alta. Recentemente propúxose o pretratamento do ferro fundido. Xa falei moito deste aspecto e publiquei moitos artigos. Non o vou repetir. Só quero combinar a fundición específica do tambor de freo e presentar algúns comentarios para a súa referencia
2. Respecto á cuestión da concepción
O propósito de inocular o ferro líquido do tambor de freo é o mesmo que producir outras pezas de ferro fundido de alta calidade. Debe garantir principalmente que non apareza cementita ou que a cantidade total de ferrita e carburo non supere o 5% para garantir unha boa forma de grafito. (Xeralmente estipúlase que un grafito debe ser superior ao 80%. O grafito B, D, E non debe ser superior ao 20%) para garantir boas propiedades mecánicas e, ao mesmo tempo, mellorar a mecanización na práctica de produción de gris ferro fundido, a súa inoculación é xeralmente de 0.2 Entre o% -0.6%. O que quero lembrar a todos neste momento é, por favor, preste atención á fertilidade e controla a fertilidade. Porque na mente da maioría dos técnicos e traballadores de fundición in situ, a maioría deles está preocupada por como mellorar o efecto de inoculación, como aumentar o núcleo de grafito e como usar inoculantes eficientes. A produción de fundición gris tamén é a mesma que a produción de ferro dúctil. Emprega varias inoculacións e usa o maior número de inoculantes posibles, ignorando o efecto da inoculación sobre as propiedades de contracción do ferro fundido gris. E esquece que as cavidades de contracción e a porosidade representaron unha gran parte dos produtos de refugallo do tambor de freo e non hai ningunha conexión entre os produtos de refugallo de contracción e o fallo anormal do tambor de freo.
Todos sabemos que, ademais dos tambores de freo desfeitos producidos por varias fábricas, moitas pezas fundidas cualificadas no almacén teñen buratos de contracción e defectos de contracción e a maioría dos técnicos do fabricante só deten as medidas para resolver a porosidade da contracción. Baixa a temperatura de vertido e mellora o deseño do sistema de vertido. Estou aquí para contarllo a todos. Débese prestar máis atención e control ao proceso de incubación do tambor de freo.
Moita xente xa se deu conta de que a inoculación pode promover a porosidade da contracción. No rango de carbono equivalente ao 3.9-4.3%, o tamaño das pezas fundidas inoculadas é sempre maior que as pezas fundidas infértiles. As pezas fundidas infértiles non teñen porosidade de contracción, pero as pezas fundidas inoculadas producen un encollemento solto. Polo tanto, na produción de tambores de freo, é necesario controlar que a cantidade de inoculación non sexa demasiado grande. Coa condición de asegurarse de que non apareza cementita e de garantir o rendemento do mecanizado, procure engadir o menos inoculante posible e non excesivo se é suficiente. O punto clave é facelo ben coa inoculación do fluxo. Non tome dúas, tres nin sequera catro xestacións durante o proceso.
3. Respecto á estanquidade do molde
A cavidade de contracción interna e a porosidade das pezas fundidas de ferro e a retracción superficial das pezas fundidas están afectadas en gran parte polo molde. Despois de verter o ferro fundido no molde, o volume da cavidade moverá a parede do molde baixo a presión estática e a calor do ferro fundido, o que fará que o volume do molde se faga maior e o tamaño da fundición estar fóra de tolerancia e o peso aumentará. O tamaño da deformación depende da compacidade do molde de area, do material de moldaxe e dos parámetros de rendemento da area. Algunhas persoas no estranxeiro investigaron nesta área. Extraen o tambor de freo da liña de produción de moldes, miden o seu tamaño e pesan o seu peso. Os resultados mostraron que o peso de cada mostra fluctúa moito. Como se mostra na seguinte figura, o peso do tambor do freo oscila entre 162 e 173 libras e a diferenza máxima é de 11 libras (1 libra é 453 gramos). A liña de moldaxe do tambor de freo de proba é a máquina de moldaxe a presión de choque. Esta diferenza de peso indica que a calidade do molde fluctúa. O molde brando impactado pola area produciu un forte abultamento da area. Para moldes con boa compacidade, o inchazo é moi lixeiro e o tamaño das pezas fundidas é preciso. Descubriron que o tambor de freo con forte inchazo ten contracción no seu interior e a calidade do tambor de freo con peso normal é normal. Polo tanto, empregaron este método de inspección sinxelo para xulgar a contracción interna do tambor do freo pesando antes de transportalo ao mecanizado e creron que a contracción do tambor do freo foi causada polo movemento do molde. Polo tanto, mellorar a rixidez do molde convértese nunha medida importante para evitar a contracción e a solta do tambor de freo.
O uso de tambores de freo cubertos de area de ferro para producir tambores de freo agora promovidos en China non ten defectos de contracción debido ás súas características. Unha empresa de grande porte en Shanxi que adopta este proceso para producir tambores de freo. Houbo tres liñas de revestimento de area semimecanizadas de ferro, con máis de 430 bidóns de freos Nissan. A taxa de rendemento do proceso é do 90% e a taxa de cualificación do produto é estable no 98%. Actualmente estase a instalar a cuarta liña de recubrimento con area tipo ferro.
Unha fábrica en Nanyang, na provincia de Henan, utiliza area de resina para producir tambores de freo pesados de Beiben con inxección superior e sen tecnoloxía elevadora, con calidade estable e sen contracción.
Nalgunhas fábricas, a distancia entre o canalón e o tambor de freo é demasiado próxima, que é de 40 mm. Aquí é difícil esmagar a area de moldaxe, polo que a miúdo se producen buracos de contracción e porosidade. A distancia cambia a 60-80mm, a porosidade de contracción É moito máis lixeira.
Algunhas pequenas fábricas primeiro golpean a area no seu conxunto e despois empregan a varilla de aceiro para inserir o arroz para facer o molde completo aínda máis axustado e fácil de golpear, o que reflicte que a contracción da fundición non é grave.
Mantén a fonte e o enderezo deste artigo para reimprimilos: O proceso de produción do tambor de freo para camión
Minghe Compañía de Fundición a Presión dedícanse á fabricación e proporcionan pezas de fundición de calidade e alto rendemento (a gama de pezas de fundición a presión de metal inclúe principalmente Fundición a presión de parede delgada,Fundición a cámara quente,Fundición a cámara fría), Servizo redondo (servizo de fundición a presión,Cnc mecanizado,Fabricación de moldes, Tratamento de superficie). Calquera requirimento de fundición a presión de aluminio, magnesio ou fundición de Zamak / cinc e outros requisitos de fundición son benvidos para poñerse en contacto connosco.
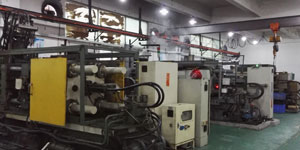
Baixo o control de ISO9001 e TS 16949, todos os procesos lévanse a cabo a través de centos de máquinas de fundición a presión avanzadas, máquinas de 5 eixes e outras instalacións, que van dende as blasters ata as lavadoras Ultra Sonic. Minghe non só ten equipos avanzados senón que tamén ten profesionais equipo de enxeñeiros, operadores e inspectores experimentados para facer realidade o deseño do cliente.
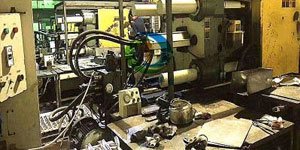
Fabricante por contrato de pezas fundidas. As capacidades inclúen pezas de fundición de aluminio a cámara fría de 0.15 libras. ata 6 libras, configuración rápida de cambio e mecanizado. Os servizos de valor engadido inclúen o pulido, vibración, desbarbado, granallado, pintura, revestimento, revestimento, montaxe e ferramentas. Entre os materiais traballados inclúense aliaxes como 360, 380, 383 e 413.
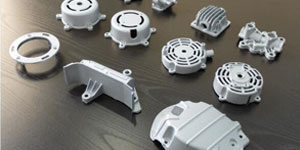
Servizos de enxeñaría simultánea de asistencia ao deseño de fundición por cinc. Fabricante a medida de pezas de fundición de cinc de precisión. Pódense fabricar pezas fundidas en miniatura, pezas fundidas de alta presión, pezas de molde de varias diapositivas, pezas de molde convencionais, pezas de moldaxe de pezas individuais e pezas de fundición independentes e pezas de fundición seladas. As pezas fundidas pódense fabricar en lonxitudes e anchuras de ata 24/0.0005 polgadas +/- XNUMX polgadas de tolerancia.
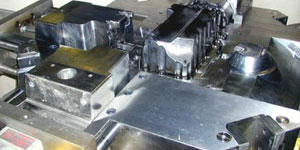
Fabricante certificado ISO 9001: 2015 de magnesio fundido a presión, as capacidades inclúen fundición a presión de magnesio de alta presión ata cámara quente de 200 toneladas e cámara fría de 3000 toneladas, deseño de ferramentas, pulido, moldeado, mecanizado, pintura en po e líquido, QA completo con capacidades CMM , montaxe, embalaxe e entrega.
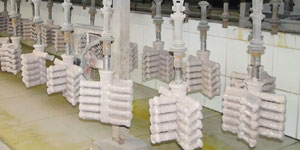
Certificado ITAF16949. Inclúe servizo de fundición adicional fundición de investimento,fundición de area,Fundición por gravidade, Fundición de escuma perdida,Fundición centrífuga,Fundición ao baleiro,Fundición permanente de moldesAs capacidades inclúen EDI, asistencia en enxeñaría, modelado sólido e procesamento secundario.
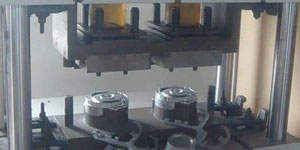
Industrias de fundición Estudos de casos de pezas para: coches, bicicletas, avións, instrumentos musicais, motos acuáticas, dispositivos ópticos, sensores, modelos, dispositivos electrónicos, caixas, reloxos, maquinaria, motores, mobles, xoias, discos, telecomunicacións, iluminación, dispositivos médicos, dispositivos fotográficos, Robots, esculturas, equipos de son, equipos deportivos, ferramentas, xoguetes e moito máis.
Que podemos axudarche a facer a continuación?
∇ Ir á páxina de inicio para China Fundición a Presión
→Pezas de fundición-Descubre o que fixemos.
→ Consellos recomendados sobre Servizos de fundición a presión
By Fabricante de fundición a presión Minghe | Categorías: Artigos útiles |material tags: Fundición de aluminio, Fundición de cinc, Fundición de magnesio, Fundición de titanio, Fundición de aceiro inoxidable, Fundición de latón,Fundición de bronce,Emisión de vídeo,Historia da empresa,Fundición en aluminio | Comentarios desactivados