Exemplos de aplicacións de area de cromita na produción de fundición
A area de cromita pertence á categoría de area especial en materiais de modelado. A súa principal composición mineral é FeO.Cr2O3, a densidade é de 4.0 ~ 4.8 g / cm3, a dureza de Mohs é de 5.5 ~ 6, a refractariedade é superior a 1900 ℃, a cromita A area ten boa resistencia á escoria alcalina e non reacciona químicamente co óxido de ferro. Dado que a condutividade térmica da area de cromita é varias veces maior que a da sílice e a sinterización en fase sólida ocorre durante o vertido de metais fundidos, é beneficioso evitar a penetración do metal fundido. Segundo estas vantaxes da area de cromita, aplicala á produción de varias pezas fundidas pode resolver os problemas de calidade de fundición de moitos produtos. A nosa empresa conseguiu moitas aplicacións exitosas en moitos produtos, como soportes de vehículos ferroviarios e cadros laterais, reixa de pantalla fixa para máquina de sinterización, forro do molino de bolas, palas eléctricas e moitos outros produtos.
Os soportes e os marcos laterais dos vehículos ferroviarios son os compoñentes principais da parte de rodaxe dos vehículos ferroviarios, así como importantes pezas que soportan tensións durante o funcionamento do vehículo. O tamaño do esquema é grande, a estrutura é complexa e os requisitos de tecnoloxía de procesos son estritos. Nalgunhas esquinas), a inspección de partículas magnéticas descubriu que había defectos de micro-fisuras e a inspección anatómica atopou defectos de contracción na intersección da parede e a parede nalgunhas partes. Segundo a análise, en comparación con outras pezas, estas pezas son os "puntos quentes" formados pola calor do aceiro fundido e a velocidade de arrefriamento das pezas adxacentes é diferente e a solidificación é tardía cando se dificulta a contracción de arrefriamento e solidificación.
Cando o esforzo interno é maior que o límite de resistencia do material metálico, a fundición producirá defectos de micro-fisuras. Cando estas pezas non se poden complementar con aceiro fundido antes da solidificación, xéranse facilmente defectos de contracción. Para eliminar estes defectos, os técnicos de fundición da nosa empresa estipulan que se debería colocar algunha area de cromita de silicato de sodio nestas pezas durante o deseño do proceso. Debido a que a condutividade térmica da area de cromita é varias veces maior que a da sílice, pode producirse. A velocidade de solidificación desta peza equilibrase coa velocidade de solidificación das partes adxacentes e elimínanse as microfisuras e os defectos de contracción xerados nestas partes.
A reixa de pantalla fixa é unha peza de reposición vulnerable na máquina de sinterización e a condición de traballo é soportar o impacto e o desgaste da sinterización a alta temperatura. A barra de reixa fixa pertence á fundición da estrutura da placa. Os buracos longos, profundos e estreitos a través da tira distribúense uniformemente sobre a fundición. Cando a barra de reixa fixa da pantalla é producida polo método tradicional de fundición en area, os buracos de tira penetrantes poden formarse polo núcleo de area. Non obstante, o proceso de funcionamento deste esquema tecnolóxico é demasiado complicado e os buracos de franxa dos moldes son facilmente bloqueados por area pegañenta, o cal é moi difícil de limpar, o que resulta nunha alta taxa de rexeitamento dos moldes. Os técnicos de fundición da nosa empresa decidiron adoptar a tecnoloxía de fundición de escuma perdida para a produción. Durante o deseño do proceso, estipulouse que os buratos da tira no molde de escuma da reixa fixa de pantalla deberían encherse de area de cromita bruta durante a vibración da caixa. Dado que a propia area de cromita sofre unha sinterización en fase sólida durante o proceso de vertido de metais fundidos, é beneficioso evitar a penetración do metal fundido, evitando así que os buratos da tira sexan bloqueados pola area pegañenta. Utilizando fundición de escuma perdida e utilizando as vantaxes do mineral de cromita, a nosa empresa produciu con éxito produtos de reixa fixa. A parede do burato da tira é lisa e plana e o tamaño é preciso. Despois da instalación e uso na máquina de sinterización, o efecto é bo, o que pode satisfacer as necesidades da produción de sinterización. .
O forro do muíño de bolas é a parte principal do muíño de bolas empregado na produción de minas metalúrxicas. Está feito de aceiro de baixa aliaxe. A estrutura é unha fundición de placas con crestas de onda levantada. Dous buratos de parafuso de montaxe están distribuídos uniformemente no forro. Os buratos dos parafusos teñen grandes buratos. , A abaixo inferior é pequena. Debido a que a parede de fundición ao redor do burato do parafuso é moi grosa, o aceiro fundido solidifícase lentamente despois de verter, de xeito que a área ao redor do burato do parafuso estea durante moito tempo nun estado de alta temperatura. A area de silicato de sodio úsase para facer o núcleo de area do burato do parafuso. Despois de verter, o burato adoita estar bloqueado por area pegañenta, moi limpa. É difícil e, despois de usar o núcleo de area de cromita de vidro de auga, aproveita a sinterización en fase sólida durante o proceso de vertido de metais fundidos a alta temperatura e pode evitar a penetración do metal fundido. A rugosidade da superficie e o tamaño do burato do parafuso do taboleiro de fundición fundido A precisión cumpre os requisitos técnicos especificados e o efecto de instalación no muíño de bolas é bo, resolvendo con éxito o problema da difícil limpeza do burato do parafuso.
A engrenaxe de pala eléctrica require que os dentes en branco sexan fundidos directamente. A área circundante entre os dentes e os dentes ten unha parede de fundición máis grosa. Despois de verter, está rodeado de metal fundido a alta temperatura. Ademais do efecto calor do ascensor superior, úsase area de sílice de vidro. Durante a fundición, a area que se pega na raíz do dente fundido é grave e non se pode garantir a forma e o tamaño do dente fundido despois de empregar o arco. Neste sentido, os técnicos de fundición da nosa empresa decidiron utilizar a tecnoloxía de fundición de escuma perdida para a produción. Despois de pintar e secar o molde branco do engrenaxe empurrando, a area de cromita bátese con vaso de auga entre os dentes de fundición e despois sopla O CO2 endurécese e logo o molde branco con area de cromita de silicato sódico embálase na caixa. Despois de verter, a area de cromita cae limpa, a superficie do dente fundido é lisa e limpa e a forma e a precisión dimensional cumpren os requisitos especificados.
Aínda que a area de cromita ten efectos obvios na eliminación de micro-gretas, pegados de area e defectos de encollemento nas pezas fundidas, o uso inadecuado tamén pode causar problemas. A impureza nociva na area de cromita é o carbonato, que descompón CO2 cando entra en contacto con metal fundido a alta temperatura, provocando poros na superficie do molde. Polo tanto, o mineral de cromita debe tostarse a unha temperatura elevada de 900-950 ° C antes da súa preparación e usalo para descompoñer o carbonato nel e despois procesalo e dividilo nun determinado tamaño de partícula. A area de cromita almacenada durante moito tempo e cuxa perda de ignición supera o estándar debería calcinarse a alta temperatura antes do seu uso.
Para garantir os requisitos de calidade da area de mineral de cromita en bruto, é necesaria unha inspección estrita da area de mineral de cromita que entra na planta segundo a normativa. En primeiro lugar, cando o mineral de cromita entra na fábrica, é necesario comprobar os seus documentos técnicos cualificados. Se está sen cualificación ou sen documentos técnicos, está prohibido entrar na fábrica; a aparición do mineral de cromita na fábrica debe manterse pura e non mesturada con impurezas; finalmente faise unha inspección de mostraxe de indicadores físicos e químicos. As condicións técnicas que deben cumprir os resultados da inspección son: tamaño de partícula de area bruta 30/50 malla, Cr2O3≥45%, SiO2≤5%, CaO≤1%, ignición perda ≤1%, refractariedade 1600 ~ 1800 ℃.
Para garantir o efecto de uso da area de cromita de silicato de sodio, ademais da area de cromita en bruto que cumpre as condicións técnicas especificadas, os requisitos técnicos que debe cumprir o silicato de sodio usado son: módulo 2.20 ± 2.40, grao de Baume 48 ~ 52 ° Sexa, Materia insoluble en auga <0.8%. Os requisitos de rendemento da area de acabado mixta: permeabilidade ao aire ≥250; forza mollada 0.05 ~ 0.09MPa; humidade ≤5%; resistencia á tracción seca 1.2 ~ 3.5MPa.
Para alcanzar os indicadores de rendemento prescritos da area de cromita de silicato de sodio, débense aplicar rigorosamente as seguintes regulacións do proceso de preparación da area de cromita.
Antes de moer, comprobe se o mecanismo de funcionamento do muíño de area é normal. O espazo entre a moa e o chasis debe ser de 10-15 mm. Preste atención á observación e axuste frecuentes; a cromita de vidro de auga mesturada no primeiro muíño despois do lavado do muíño de area Debe prestarse especial atención ao control da humidade na area. O contido de humidade do muíño non debe superar o 0.5% especificado; o operador de preparación de area de cromita de vidro de auga a miúdo debe limpar a area pegajosa da roda do muíño e manter limpo o batedor de area para garantir o vaso de auga. A area de cromita mestúrase e fresase uniformemente; os requisitos de relación de mestura son: 100% de area bruta, 2.5% a 3.5% de vaso de auga; tempo de mestura: area crúa + vidro auga mesturando de 2 a 3.5 minutos para producir area; para cada preparación Todas as areas de cromita de silicato sódico deben ser probadas para determinar as propiedades físicas e os técnicos de fundición deben comprender os resultados das probas para atopar problemas e tratar con eles a tempo.
Mantén a fonte e o enderezo deste artigo para reimprimilos: Exemplos de aplicacións de area de cromita na produción de fundición
Minghe Compañía de Fundición a Presión dedícanse á fabricación e proporcionan pezas de fundición de calidade e alto rendemento (a gama de pezas de fundición a presión de metal inclúe principalmente Fundición a presión de parede delgada,Fundición a cámara quente,Fundición a cámara fría), Servizo redondo (servizo de fundición a presión,Cnc mecanizado,Fabricación de moldes, Tratamento de superficie). Calquera requirimento de fundición a presión de aluminio, magnesio ou fundición de Zamak / cinc e outros requisitos de fundición son benvidos para poñerse en contacto connosco.
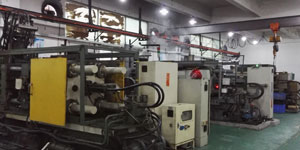
Baixo o control de ISO9001 e TS 16949, todos os procesos lévanse a cabo a través de centos de máquinas de fundición a presión avanzadas, máquinas de 5 eixes e outras instalacións, que van dende as blasters ata as lavadoras Ultra Sonic. Minghe non só ten equipos avanzados senón que tamén ten profesionais equipo de enxeñeiros, operadores e inspectores experimentados para facer realidade o deseño do cliente.
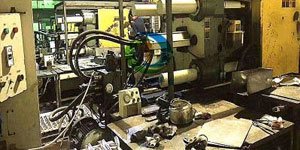
Fabricante por contrato de pezas fundidas. As capacidades inclúen pezas de fundición de aluminio a cámara fría de 0.15 libras. ata 6 libras, configuración rápida de cambio e mecanizado. Os servizos de valor engadido inclúen o pulido, vibración, desbarbado, granallado, pintura, revestimento, revestimento, montaxe e ferramentas. Entre os materiais traballados inclúense aliaxes como 360, 380, 383 e 413.
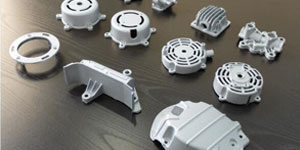
Servizos de enxeñaría simultánea de asistencia ao deseño de fundición por cinc. Fabricante a medida de pezas de fundición de cinc de precisión. Pódense fabricar pezas fundidas en miniatura, pezas fundidas de alta presión, pezas de molde de varias diapositivas, pezas de molde convencionais, pezas de moldaxe de pezas individuais e pezas de fundición independentes e pezas de fundición seladas. As pezas fundidas pódense fabricar en lonxitudes e anchuras de ata 24/0.0005 polgadas +/- XNUMX polgadas de tolerancia.
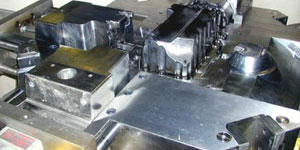
Fabricante certificado ISO 9001: 2015 de magnesio fundido a presión, as capacidades inclúen fundición a presión de magnesio de alta presión ata cámara quente de 200 toneladas e cámara fría de 3000 toneladas, deseño de ferramentas, pulido, moldeado, mecanizado, pintura en po e líquido, QA completo con capacidades CMM , montaxe, embalaxe e entrega.
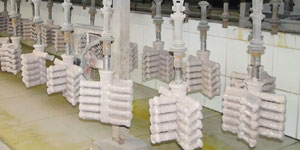
Certificado ITAF16949. Inclúe servizo de fundición adicional fundición de investimento,fundición de area,Fundición por gravidade, Fundición de escuma perdida,Fundición centrífuga,Fundición ao baleiro,Fundición permanente de moldesAs capacidades inclúen EDI, asistencia en enxeñaría, modelado sólido e procesamento secundario.
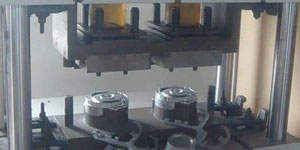
Industrias de fundición Estudos de casos de pezas para: coches, bicicletas, avións, instrumentos musicais, motos acuáticas, dispositivos ópticos, sensores, modelos, dispositivos electrónicos, caixas, reloxos, maquinaria, motores, mobles, xoias, discos, telecomunicacións, iluminación, dispositivos médicos, dispositivos fotográficos, Robots, esculturas, equipos de son, equipos deportivos, ferramentas, xoguetes e moito máis.
Que podemos axudarche a facer a continuación?
∇ Ir á páxina de inicio para China Fundición a Presión
→Pezas de fundición-Descubre o que fixemos.
→ Consellos recomendados sobre Servizos de fundición a presión
By Fabricante de fundición a presión Minghe | Categorías: Artigos útiles |material tags: Fundición de aluminio, Fundición de cinc, Fundición de magnesio, Fundición de titanio, Fundición de aceiro inoxidable, Fundición de latón,Fundición de bronce,Emisión de vídeo,Historia da empresa,Fundición en aluminio | Comentarios desactivados