Varios problemas aos que hai que prestar atención na fundición de area de silicato de sodio
1 Cales son os factores que afectan ao "envellecemento" do vaso de auga? Como eliminar o "envellecemento" do vaso de auga?
O vaso de auga recentemente preparado é unha verdadeira solución. Non obstante, durante o proceso de almacenamento, o ácido silícico no vaso de auga experimentará unha polimerización por condensación, que gradualmente se condensará da verdadeira solución nunha solución de ácido silícico macromolecular e, finalmente, converterase nun xel de ácido silícico. Polo tanto, o vaso de auga é realmente unha mestura heteroxénea composta de ácido polisílico con diferentes graos de polimerización, que é facilmente afectada polo seu módulo, concentración, temperatura, contido de electrolitos e tempo de almacenamento.
Durante o almacenamento, as moléculas do vaso de auga sofren polimerización por condensación para formar un xel e a súa forza de unión diminúe gradualmente coa extensión do tempo de almacenamento. Este fenómeno chámase "envellecemento" do vaso de auga.
O fenómeno do "envellecemento" pode explicarse polos seguintes dous conxuntos de datos de proba: vaso de auga de alto módulo (M = 2.89, ρ = 1.44g / cm3) despois de 20, 60, 120, 180, 240 días de almacenamento, o CO2 endurecido bótase un vaso de auga. A resistencia á tracción seca da area cae dun 9.9%, 14%, 23.5%, 36.8% e 40%; o silicato sódico de baixo módulo (M = 2.44, ρ = 1.41 g / cm3) almacénase durante 7, 30, 60 e 90 días despois de ser secado. A resistencia á tracción diminuíu un 4.5%, 5%, 7.3% e 11% respectivamente.
O tempo de almacenamento do vaso de auga ten pouco efecto sobre a resistencia inicial da area de endurecemento do vidro de auga endurecido por éster, pero ten un efecto significativo sobre a resistencia posterior. Segundo as medicións, redúcese aproximadamente nun 60% para o vaso de auga de alto módulo e nun 15-20% para o vaso de auga de módulo baixo. . A forza residual tamén diminúe coa extensión do tempo de almacenamento.
Durante o almacenamento do vaso de auga, a policondensación e a despolimerización do ácido polisílico continúan ao mesmo tempo, o peso molecular desproporcionase e, finalmente, fórmase un sistema multi-disperso no que coexisten o ácido monoortosílico e as partículas coloidais. É dicir, durante o proceso de envellecemento do vaso de auga, o grao de polimerización do ácido silícico é desproporcionado e o contido de ácido monoortosílico e ácido polisílico elevado aumenta coa extensión do tempo de almacenamento. Como resultado da reacción de polimerización por condensación e despolimerización do vaso de auga durante o almacenamento, a forza de unión redúcese, é dicir, prodúcese o fenómeno do "envellecemento".
Os principais factores que afectan ao "envellecemento" do vaso de auga son: o tempo de almacenamento, o módulo e a concentración do vaso de auga. Canto máis tempo de almacenamento, maior módulo e maior concentración, máis grave é o "envellecemento".
O vaso de auga de longa existencia pódese modificar de varias formas para eliminar o "envellecemento" e restaurar o vaso de auga ao rendemento do vaso de auga doce:
1. Modificación física
O envellecemento do vaso de auga é un proceso espontáneo que libera lentamente enerxía. A modificación física do vaso de auga "envellecido" consiste en utilizar campo magnético, ultrasóns, alta frecuencia ou calefacción para proporcionar enerxía ao sistema de vidro de auga e promover a alta polimerización da cola de polisilicato. As partículas volven a despolimerizar e promoven a homoxeneización do peso molecular do ácido polisílico, eliminando así o fenómeno do envellecemento, que é o mecanismo da modificación física. Por exemplo, despois do tratamento cun campo magnético, a forza da area de silicato de sodio aumenta nun 20-30%, a cantidade de silicato de sodio engadida redúcese nun 30-40%, afórrase CO2, mellórase a colapsabilidade e hai boas beneficios económicos.
A desvantaxe da modificación física é que non é duradeira e a forza de unión diminuirá cando se almacene despois do tratamento, polo que é adecuada para o seu uso o antes posible despois do tratamento na fundición. Especialmente para o vaso de auga con M> 2.6, a concentración de moléculas de ácido silícico é grande e, despois da modificación física e da despolimerización, policondensará relativamente rápido. É mellor usalo inmediatamente despois do tratamento.
2. Modificación química
A modificación química consiste en engadir unha pequena cantidade de compostos ao vaso de auga, todos estes compostos conteñen carboxilo, amida, carbonilo, hidroxilo, éter, amino e outros grupos polares, que se adsorben sobre moléculas de ácido silícico ou partículas coloidais a través de enlaces de hidróxeno ou estáticos. electricidade. Superficie, cambia a súa enerxía potencial superficial e capacidade de solvatación, mellora a estabilidade do ácido polisílico, evitando así que continúe o "envellecemento".
Por exemplo, engadir poliacrilamida, amidón modificado, polifosfato, etc. ao vaso de auga pode obter mellores resultados.
Incorporar materia orgánica ao vaso de auga común ou incluso ao vaso de auga modificado pode desempeñar unha variedade de funcións, como: cambiar as propiedades do fluxo viscoso do vaso de auga; mellorar o rendemento de modelado de mesturas de vidro de auga; aumentando a forza de unión para facer o vaso de auga absolutamente engadido A cantidade redúcese; mellórase a plasticidade do xel de ácido silícico; a resistencia residual redúcese, de xeito que a area do vidro de auga é máis axeitada para fundicións e aliaxes non férreas.
3. Modificación físico-química
A modificación física é adecuada para o vaso de auga "envellecido" e pode usarse inmediatamente despois da modificación. A modificación química é axeitada para procesar o vaso de auga doce e o vaso de auga modificado pode almacenarse durante moito tempo. A combinación de modificación física e modificación química pode facer que o vaso de auga teña un efecto de modificación duradeira. Por exemplo, engadir poliacrilamida ao autoclave para modificar o vaso de auga "envellecido" ten un bo efecto. Entre eles utilízanse a presión e a presión do autoclave. A axitación é unha modificación física e a adición de poliacrilamida é unha modificación química.
2 Como evitar que o CO2 sufra silicato de sodio endurecido con moldes de area (núcleo) de tiza?
Despois de que a area de silicato sódico de sodio se endureza co CO2 e se deixe por un período de tempo, ás veces aparecerá unha substancia como a xeadas na superficie do molde inferior (núcleo), o que reducirá seriamente a resistencia superficial do lugar e producirá facilmente area defectos de lavado durante a vertedura. Segundo a análise, o compoñente principal desta substancia branca é o NaHCO3, que pode ser causado por unha humidade excesiva ou CO2 na area de silicato de sodio. A reacción é a seguinte:
Na2CO3 + H2O → NaHCO3 + NaOH
Na2O+2CO2+H2O→2NaHCO3
NaHCO3 migra facilmente cara a fóra coa humidade, provocando xeadas como a superficie na superficie do molde e do núcleo.
A solución é a seguinte:
1. Controle que o contido de humidade da area de silicato de sodio non sexa demasiado alto (especialmente na estación das choivas e no inverno).
2. O tempo para soprar CO2 non debe ser demasiado longo.
3. O molde e o núcleo endurecidos non se deben colocar durante moito tempo e deben moldearse e botarse a tempo.
4. Engadir aproximadamente un 1% (fracción en masa) do xarope cunha densidade de 1.3 g / cm3 á area de silicato sódico pode evitar que a superficie se po.
3 Como mellorar a resistencia á absorción de humidade do molde de area de vidro de auga (núcleo)?
O núcleo de area de vidro con auga de sosa endurecido por CO2 ou métodos de calefacción está ensamblado no molde de barro mollado. Se non se verte no tempo, a forza do núcleo de area diminuirá bruscamente, non só pode arrastrarse, incluso derrubarse; almacénase nun ambiente húmido A forza do núcleo de area tamén se reduce significativamente. A táboa 1 mostra o valor de forza do núcleo de area de vidro de auga de sodio endurecido con CO2 cando se coloca nun ambiente cunha humidade relativa do 97% durante 24 horas. O motivo da perda de forza cando se almacena nun ambiente húmido débese á rehidratación do vaso de sodio. O Na + e o OH na matriz do aglutinante de silicato de sodio absorben a humidade e erosionan a matriz, rompendo finalmente o enlace silicio-osíxeno Si-O-Si, o que resulta nunha diminución significativa da forza de unión da area de silicato de sodio.
1. O vaso de auga de litio engádese ao vaso de sodio ou Li2CO3, CaCO3, ZnCO3 e outros aditivos inorgánicos engádense ao vaso de auga de sodio, porque se poden formar carbonatos e silicatos relativamente insolubles e pódense reducir ións de sodio libres. pódese mellorar a resistencia á absorción do aglutinante de vidro de sodio.
2. Engade unha pequena cantidade de materia orgánica ou materia orgánica con función tensioactiva ao vaso de auga de sodio. Cando o aglutinante se endurece, os ións hidrofílicos Na + e OH- no xel de auga de sodio poden ser substituídos por grupos hidrofóbicos orgánicos ou, combinados entre si, a base hidrofóbica orgánica exposta mellora a absorción de humidade.
3. Mellora o módulo do vaso de auga porque a resistencia á humidade do vaso de auga de alto módulo é máis forte que a do vaso de auga de módulo baixo.
4. Engade hidrolizado de amidón á area de silicato de sodio. Un método mellor é usar hidrolizado de amidón para modificar o vaso de auga de sodio.
4 Cales son as características do proceso composto de auga endurecida por vento de CO2 con resina fenólica alcalina e resina fenólica?
Nos últimos anos, para mellorar a calidade das pezas fundidas de aceiro, algunhas pequenas e medianas empresas precisan adoptar con urxencia o proceso de area de resina. Non obstante, debido á capacidade económica limitada, non poden mercar equipos de rexeneración de area de resina e a area vella non se pode reciclar, o que resulta en custos de produción elevados. Para atopar un xeito eficaz de mellorar a calidade das pezas fundidas sen aumentar demasiado o custo, pódense combinar as características do proceso de area de silicato de sodio endurecido por soprado de CO2 e area de resina fenólica alcalina endurecida por soplado de CO2 e de silicato de sodio endurecido por sopro de CO2 pódese empregar resina fenólica. O proceso de composto de area de resina emprega area de resina fenólica alcalina como area superficial e area de vidro de auga como area traseira, mentres sopra CO2 para endurecerse.
A resina fenólica empregada na area de resina fenólica alcalina ao CO2 prodúcese por policondensación de fenol e formaldehído baixo a acción dun forte catalizador alcalino e engadindo un axente de acoplamento. O seu valor PH é ≥13 e a súa viscosidade é ≤500mPa • s. A cantidade de resina fenólica engadida á area é do 3% ao 4% (fracción de masa). Cando o caudal de CO2 é de 0.8 ~ 1.0 m3 / h, o mellor tempo de soprado é de 30 ~ 60 s; se o tempo de soprado é demasiado curto, a forza de endurecemento do núcleo de area será baixa; se o tempo de soprado é demasiado longo, a forza do núcleo de area non aumentará e é gas perdido.
CO2: a area de resina fenólica alcalina non contén elementos nocivos como N, P, S, etc., polo que se eliminan os defectos de fundición como poros, microfisuras superficiais, etc. causados por estes elementos; gases nocivos como H2S e SO2 non se liberan durante o vertido, o que é beneficioso para a protección do ambiente; Boa plegabilidade, fácil de limpar; alta precisión dimensional; alta eficiencia de produción.
O proceso composto de auga endurecida por resina fenólica alcalina de vidro endurecido con CO2 pode ser amplamente utilizado en pezas fundidas de aceiro, ferro fundido, aliaxes de cobre e pezas fundidas de aliaxe lixeira.
O proceso composto é un proceso sinxelo e cómodo. O proceso é o seguinte: primeiro mestura area de resina e area de silicato de sodio por separado e logo colócaos en dous cubos de area; despois engade a area de resina mesturada como area superficial na caixa de area e quilos, o espesor da capa de area superficial é xeralmente de 30-50 mm; despois engádese area de vidro auga para que a area traseira se encha e se compacte; finalmente, o gas CO2 é soprado no molde para o seu endurecemento.
O diámetro do tubo de soplado é xeralmente de 25 mm e o alcance endurecible é aproximadamente 6 veces o diámetro do tubo de soplado.
O tempo de soprado depende do tamaño, a forma, o fluxo de gas e a área do tapón de escape do molde de area (núcleo). Xeralmente, o tempo de soprado contrólase dentro dos 15 ~ 40s.
Despois de soprar o molde de area dura (núcleo), pódese tomar o molde. A forza do molde de area (núcleo) aumenta rapidamente. Cepille a pintura dentro de media hora despois de tomar o molde e pecha a caixa para verter despois de 4 horas.
O proceso composto é especialmente adecuado para plantas de fundición de aceiro que non dispoñen de equipos de rexeneración de area de resina e que precisan producir pezas fundidas de alta calidade. O proceso é sinxelo e doado de controlar, e a calidade das pezas fundidas producidas é equivalente á doutras pezas fundidas con area de resina.
A area de silicato de sodio endurecido por vento por CO2 tamén se pode combinar con area de resina de poliacrilato de sodio endurecido por vento por CO2 para a produción de varias pezas fundidas de alta calidade.
5 Cales son os pros e os contras do proceso de area de silicato de sodio endurecido composto de éster orgánico CO2?
Nos últimos anos, o proceso de area de silicato de sodio endurecido composto de éster orgánico de CO2 ten unha tendencia de expansión das aplicacións. O proceso é o seguinte: engade unha certa cantidade de éster orgánico durante a mestura de area (normalmente a metade da cantidade normal requirida ou 4 ~ 6% do peso do vaso de auga); despois de completar o modelado, sopre o CO2 para endurecer a forza de liberación do molde (normalmente é necesaria resistencia á compresión) A forza é de aproximadamente 0.5 MPa); despois do desmoldado, o éster orgánico segue endurecéndose e a forza da area de moldaxe aumenta a un ritmo máis rápido; despois de soprar o CO2 e colocalo durante 3 ~ 6h, pódese combinar e verter o molde de area.
O mecanismo de endurecemento é:
Cando a area de vidro de auga sopra CO2, baixo a acción da diferenza de presión do gas e a diferenza de concentración, o gas CO2 intentará fluír en todas as direccións da area de moldaxe. Despois de que o gas CO2 entre en contacto co vaso de auga, reacciona inmediatamente con el para formar un xel. Debido ao efecto de difusión, a reacción é sempre do exterior cara ao interior e a capa externa primeiro forma unha película de xel, que impide que o gas CO2 e o vaso de auga sigan reaccionando. Polo tanto, en pouco tempo, independentemente do método empregado para controlar o CO2, é imposible facelo reaccionar con todo o vaso de auga. Segundo a análise, cando a area de moldaxe alcanza a mellor forza de soplado, o vaso de auga que reaccionou co CO2 é de aproximadamente o 65%. Isto significa que o vaso de auga non exerce por completo o seu efecto de unión e polo menos o 35% do vaso de auga non reacciona. O endurecedor de éster orgánico pode formar unha mestura uniforme co ligante e pode dar un xogo completo ao efecto de unión do ligante. Todas as partes da area do núcleo acumulan forza á mesma velocidade.
Aumentar a cantidade de vaso de auga engadido aumentará a resistencia final do molde de area, pero a súa resistencia residual tamén aumentará, dificultando a limpeza da area. Cando a cantidade engadida de vaso de auga é demasiado pequena, a forza final é demasiado pequena e non pode cumprir os requisitos para o seu uso. Na produción real, a cantidade de vaso de auga engadida contrólase xeralmente nun 4% aproximadamente.
Cando se usa só éster orgánico para endurecer, a cantidade xeral de éster orgánico engadida é do 8 ao 15% da cantidade de vaso de auga. Cando se usa endurecemento composto, calcúlase que aproximadamente a metade do vaso de auga endureceuse cando se sopra o CO2 e aproximadamente a metade do vaso de auga aínda non se endureceu. Polo tanto, é máis apropiado que a cantidade de ésteres orgánicos supoña entre o 4 e o 6% da cantidade de vaso de auga.
O método de endurecemento composto pode dar un xogo completo ás dobre vantaxes do endurecemento por CO2 e o endurecemento por éster orgánico e pode exercer plenamente o efecto de unión do vaso de auga para acadar unha velocidade de endurecemento rápida, liberación precoz do molde, alta resistencia, boa colapsabilidade e baixo custo. Efecto integral.
Non obstante, o proceso de endurecemento composto de éster orgánico CO2 ten que engadir un 0.5 a un 1% máis de vidro de auga que o método de endurecemento de éster orgánico simple, o que aumentará a dificultade de rexeneración da area de vidro de auga usada.
6 Por que é doado producir area pegañenta cando se utiliza o proceso de area de silicato de sodio para producir pezas fundidas de ferro? Como previlo?
Cando se usa o molde de area (núcleo) de area de silicato de sodio para verter fundicións de ferro, a miúdo prodúcese area pegajosa grave, o que limita a súa aplicación na produción de ferro fundido.
O Na2O, SiO2 da area de silicato de sodio e o óxido de ferro producido polo metal líquido durante o vertido forman silicato de baixa fusión. Como se mencionou anteriormente, se este composto contén vidro amorfo máis fusible, a forza de unión entre esta capa de vidro e a superficie do molde é moi pequena e o coeficiente de contracción é diferente ao do metal. O gran esforzo é fácil de eliminar da superficie do molde sen que se pegue area. Se o composto formado na superficie da fundición ten un alto contido de SiO2 e un baixo contido de FeO, MnO, etc., a súa estrutura solidificada ten basicamente unha estrutura cristalina, que se combinará firmemente coa fundición, producindo unha area pegañenta. .
Cando a area de silicato de sodio se usa para producir pezas fundidas de ferro, debido á baixa temperatura de vertido e ao alto contido en carbono das pezas fundidas, o ferro e o manganeso non se oxidan facilmente e a capa de area pegajosa resultante ten unha estrutura cristalina e é difícil para establecer unha capa adecuada entre as fundicións de ferro e a capa de area pegajosa. O espesor da capa de óxido de ferro é diferente da area de resina entre a fundición e a capa de area pegañenta, que pode producir unha película de carbono brillante a través da pirólise da resina ao producir pezas fundidas de ferro, polo que a capa de area pegañenta non é fácil de eliminar.
Para evitar a produción de area de vidro con sosa a partir da produción de pezas fundidas de ferro, pódense empregar revestimentos adecuados. Como a pintura a base de auga, hai que secar a superficie despois de pintala, polo que é mellor pintar de secado rápido a base de alcohol.
En xeral, as pezas fundidas de ferro tamén poden engadir unha cantidade adecuada de carbón en po (como o 3% ao 6%) (fracción de masa) á area de silicato de sodio, de xeito que a pirólise do carbón en po entre a fundición e a capa de area pode producir unha brillante película de carbono. Non o mollan os metais e os seus óxidos, de xeito que a capa de area pegañenta quítase fácilmente da fundición.
7 Espérase que a area de silicato de sodio se converta nunha area de moldaxe ecolóxica sen descarga de area residual?
O vaso de auga é incoloro, inodoro e non tóxico. Non causará problemas graves se toca a pel e a roupa e enxágüe con auga, pero hai que evitar salpicar os ollos. O vidro de auga non ten gases irritantes ou nocivos liberados durante a mestura, modelado, endurecemento e vertido de area, e non hai contaminación por ácido e negro. Non obstante, se o proceso é inadecuado e se engade demasiado silicato de sodio, a colapsabilidade da area de silicato de sodio non será boa e o po voará durante a limpeza da area, o que tamén causará contaminación. Ao mesmo tempo, é difícil rexenerar a area vella e a descarga de area residual provoca contaminación alcalina no ambiente.
Se estes dous problemas poden superarse, a area de silicato de sodio pode converterse nunha area de moldaxe respectuosa co medio ambiente sen descarga de area residual.
A medida fundamental para resolver estes dous problemas é reducir a cantidade de vaso de auga engadida a menos dun 2%, que basicamente pode sacudir a area. Cando se reduce a cantidade de vaso de auga engadido, tamén se reduce o Na2O residual na area vella. Usando un método de rexeneración en seco relativamente sinxelo, é posible manter o Na2O residual na area circulante por baixo do 0.25%. Esta area recuperada pode cumprir os requisitos de aplicación de area de moldaxe simple para pezas fundidas de aceiro de pequeno e mediano tamaño. Neste momento, aínda que a vella area de silicato de sodio non use o custoso e complicado método mollado para rexenerarse, pero utilízase o método seco relativamente sinxelo e barato, pódese reciclar completamente, basicamente non se descarga area residual e a relación de area a ferro Pódese reducir a menos de 1: 1.
8 Como rexenerar con eficacia a area de silicato de sodio?
Se o Na2O residual na vella area de silicato de sodio é demasiado alto, despois de engadir o silicato de sodio á area, a area de moldaxe non terá o suficiente tempo útil e a acumulación de demasiado Na2O deteriorará a refractariedade da area de cuarzo. Polo tanto, o Na2O residual debe eliminarse o máximo posible ao rexenerar a area de silicato de sodio utilizada.
Mantén a fonte e o enderezo deste artigo para reimprimilos:Varios problemas aos que hai que prestar atención na fundición de area de silicato de sodio
Minghe Compañía de Fundición a Presión dedícanse á fabricación e proporcionan pezas de fundición de calidade e alto rendemento (a gama de pezas de fundición a presión de metal inclúe principalmente Fundición a presión de parede delgada,Fundición a cámara quente,Fundición a cámara fría), Servizo redondo (servizo de fundición a presión,Cnc mecanizado,Fabricación de moldes, Tratamento de superficie). Calquera requirimento de fundición a presión de aluminio, magnesio ou fundición de Zamak / cinc e outros requisitos de fundición son benvidos para poñerse en contacto connosco.
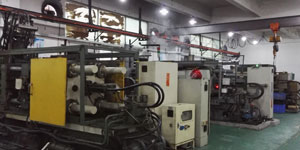
Baixo o control de ISO9001 e TS 16949, todos os procesos lévanse a cabo a través de centos de máquinas de fundición a presión avanzadas, máquinas de 5 eixes e outras instalacións, que van dende as blasters ata as lavadoras Ultra Sonic. Minghe non só ten equipos avanzados senón que tamén ten profesionais equipo de enxeñeiros, operadores e inspectores experimentados para facer realidade o deseño do cliente.
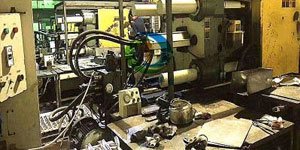
Fabricante por contrato de pezas fundidas. As capacidades inclúen pezas de fundición de aluminio a cámara fría de 0.15 libras. ata 6 libras, configuración rápida de cambio e mecanizado. Os servizos de valor engadido inclúen o pulido, vibración, desbarbado, granallado, pintura, revestimento, revestimento, montaxe e ferramentas. Entre os materiais traballados inclúense aliaxes como 360, 380, 383 e 413.
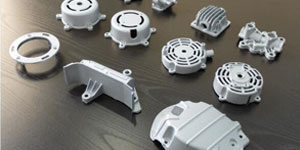
Servizos de enxeñaría simultánea de asistencia ao deseño de fundición por cinc. Fabricante a medida de pezas de fundición de cinc de precisión. Pódense fabricar pezas fundidas en miniatura, pezas fundidas de alta presión, pezas de molde de varias diapositivas, pezas de molde convencionais, pezas de moldaxe de pezas individuais e pezas de fundición independentes e pezas de fundición seladas. As pezas fundidas pódense fabricar en lonxitudes e anchuras de ata 24/0.0005 polgadas +/- XNUMX polgadas de tolerancia.
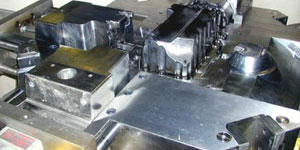
Fabricante certificado ISO 9001: 2015 de magnesio fundido a presión, as capacidades inclúen fundición a presión de magnesio de alta presión ata cámara quente de 200 toneladas e cámara fría de 3000 toneladas, deseño de ferramentas, pulido, moldeado, mecanizado, pintura en po e líquido, QA completo con capacidades CMM , montaxe, embalaxe e entrega.
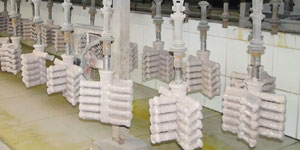
Certificado ITAF16949. Inclúe servizo de fundición adicional fundición de investimento,fundición de area,Fundición por gravidade, Fundición de escuma perdida,Fundición centrífuga,Fundición ao baleiro,Fundición permanente de moldesAs capacidades inclúen EDI, asistencia en enxeñaría, modelado sólido e procesamento secundario.
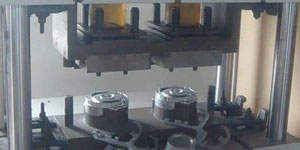
Industrias de fundición Estudos de casos de pezas para: coches, bicicletas, avións, instrumentos musicais, motos acuáticas, dispositivos ópticos, sensores, modelos, dispositivos electrónicos, caixas, reloxos, maquinaria, motores, mobles, xoias, discos, telecomunicacións, iluminación, dispositivos médicos, dispositivos fotográficos, Robots, esculturas, equipos de son, equipos deportivos, ferramentas, xoguetes e moito máis.
Que podemos axudarche a facer a continuación?
∇ Ir á páxina de inicio para China Fundición a Presión
→Pezas de fundición-Descubre o que fixemos.
→ Consellos recomendados sobre Servizos de fundición a presión
By Fabricante de fundición a presión Minghe | Categorías: Artigos útiles |material tags: Fundición de aluminio, Fundición de cinc, Fundición de magnesio, Fundición de titanio, Fundición de aceiro inoxidable, Fundición de latón,Fundición de bronce,Emisión de vídeo,Historia da empresa,Fundición en aluminio | Comentarios desactivados