Como garantir a estabilidade do sistema de area verde?
I. Introdución
Debido aos cambios nas condicións de produción e no ambiente, outros parámetros da fundición cambiarán inevitablemente. Se o proceso de moldaxe da area non se pode axustar a tempo, o sistema de area será inestable, o que acabará por levar a unha limpeza máis difícil da fundición ou incluso da chatarra;
Deste xeito, é necesario axustar o proceso orixinal de area de moldaxe para estabilizar o sistema de area; a composición material da area de moldaxe está composta principalmente por area vella, area bruta, bentonita e aditivos. Dado que máis do 95% da area de moldaxe é area vella e a area vella está afectada por factores como a diferente relación area-ferro da fundición e a diferente cantidade de mestura da area do núcleo, o que resulta en flutuacións moi grandes no a composición material. Polo tanto, para controlar a composición da area de moldaxe, é necesario inspeccionar o contido efectivo de bentonita, o contido de aditivos efectivos e o contido de barro na area de moldaxe para determinar a cantidade engadida de bentonita, aditivos e area bruta durante a mestura de area.
Este artigo introducirá brevemente como a fundición da compañía do autor está enraizada no proceso de produción real.
Segundo o cambio de parámetros, o proceso de moldaxe da area axústase para garantir a estabilidade do sistema de area.
2. Definición dos parámetros clave da area de moldaxe:
1. Contido efectivo de bentonita: o contido efectivo de bentonita (activo) determínase en función das características do mineral de montmorillonita contido na bentonita que pode absorber o azul de metileno e outros colorantes; refírese á valoración de 5.00 g de area de moldaxe cunha solución de azul de metileno puro reactivo de concentración do 0.20% [mL]; convertido segundo a fórmula estándar da curva de bentonita (%)
2. Dosificación efectiva de aditivos: compárase coa evolución dos gases dos aditivos de area de moldaxe e calcúlase empregando a fórmula; é dicir, a evolución do gas de 1.00 g de area de moldaxe a 900 ° C [mL] menos a evolución do gas da bentonita activada na area de moldaxe (a cantidade media medida antes do cálculo) A continuación compárase con 1 g de volume de gas aditivo (%).
3. Contido de barro: segundo a norma nacional GB / T9442-1998, as partículas finas de po cun diámetro inferior a 20 μm defínense como barro. Os lodos son normalmente eliminados mediante método de lavado [2].
4. Tamaño das partículas de area de moldaxe: expresado en finura AFS, é dicir, o tamaño medio das partículas de area reflíctese segundo a marca imaxinaria de peneira [3];
5. Método de cálculo de finura AFS: Os procedementos de medición de finura AFS e os métodos de cálculo especificados polo American Institute of Foundry son os seguintes:
①. Primeiro pesa uns 50 g da mostra de area que se vai medir, lave o barro, seca e despois criba
②. Pesar e rexistrar a calidade das partículas de area que quedan en cada peneira;
③. Calcula a porcentaxe da cantidade de partículas de area que queda en cada peneira á cantidade total de mostras de area;
④. Multiplica a porcentaxe da cantidade de partículas de area que quedan en cada peneira polo "multiplicador de finura AFS" correspondente a cada peneira;
⑤. Engade os produtos anteriores para cada número de peneira para atopar a suma:
⑥. Dividir a suma obtida no punto 5 pola suma das porcentaxes de area retida en cada peneira do punto 3 para obter a finura AFS
3. Plan de axuste:
O equipo de mestura de area utilizado pola fábrica é a fábrica de area DISA e a liña de moldaxe a presión estática de equipos KW; empregando estatísticas de datos durante medio ano, formuláronse os seguintes plans para o seu sistema de area de moldaxe:
1. Estatísticas:
① Determine a cantidade de area de moldaxe engadida a cada caixa segundo o valor de configuración do anfitrión de moldaxe e calcule a relación area-ferro de cada caixa de pezas fundidas segundo o peso de cada caixa de pezas fundidas e o peso da vertedura. o sistema e a cantidade de area do núcleo empregada na fundición;
②Estadísticas sobre a cantidade de area residual vertida e o uso de area de núcleo e materiais auxiliares
③ Estatísticas de eliminación de po do sistema de area de moldaxe
2. Axuste de area:
① Segundo a situación de produción, cando se produce continuamente unha fundición durante dous ou máis días, fixarase a cantidade engadida de accesorios de area de moldaxe (bentonita, aditivos) e contaranse os cambios na cantidade efectiva de area de moldaxe e despois compróbase gradualmente durante a produción continua doutras pezas fundidas. A relación entre a relación area / ferro e a cantidade engadida;
② Axuste do tamaño das partículas de area de moldaxe: axuste segundo o valor medio de peneira 50/100 (area de sílice de peneira 50/100, o valor medio da finura media é 50 [4]), cando o AFS da area de moldaxe é menor ou igual a 50, engadindo area fina 70/140 ou máis nova axústase 140/70, engádese 30 kg-60 kg por fábrica e analízase o cambio no tamaño das partículas.
③ Axuste do contido de barro da area de moldaxe: analiza o cambio do contido de barro do sistema de area de moldaxe a través das estatísticas da eliminación diaria de po;
En cuarto lugar, o proceso de axuste específico:
1. Estatísticas da relación entre area e ferro fundido:
(Nota: Dado que o corpo do cilindro X2B1 está fundido con núcleo integral de area, non queimará a area de moldaxe, polo que o peso da area de moldaxe exterior da fundición calcúlase como "0")
2. Axuste a cantidade efectiva segundo a relación area-ferro da fundición. A relación area-ferro do bloque de cilindros 56D é de 6.57. Entre as pezas fundidas anteriores, a relación area-ferro é a máis alta entre as pezas fundidas do bloque de cilindros. Polo tanto, primeiro se proba o bloque de cilindros 56D:
Cando se produciu 56D durante tres días consecutivos, a cantidade de aditivo era de 22 kg / muíño e a cantidade de aditivo de arxila era de 33 kg / muíño; a cantidade efectiva de aditivos subiu do 4.55% ao 5.03%; a cantidade efectiva de arxila subiu do 6.56% ao 7%; un aumento de aproximadamente o 0.5%; Significa que cando se produce un cilindro 56D, a cantidade engadida debe axustarse para ser superior ao valor de equilibrio do sistema de area;
A través da análise de datos anterior, a cantidade de materiais auxiliares engadidos axústase do seguinte xeito:
1) Cando se reproduce o cilindro, a cantidade de aditivo axústase a 19 kg / muíño e cando a cantidade de aditivo de arxila é de 26 kg / muíño, as estatísticas de datos durante tres días consecutivos mostran que a cantidade efectiva de aditivos cambiou do 4.36% ao 4.29% ; a cantidade efectiva de arxila cambiou do 4.36% ao 4.29%. O 7.22% convértese nun 7.11%; a cantidade efectiva oscila un 0.1%; polo tanto, o plan de axuste do proceso é razoable e pode garantir o equilibrio do sistema de area de moldaxe;
2) Do mesmo xeito, a relación entre a cantidade de materiais auxiliares engadidos a outras pezas de fundición e a cantidade efectiva calcúlase mediante a análise de datos experimentais e a teoría; ao reproducir diferentes fundicións, axuste a cantidade adecuada de materiais auxiliares engadidos.
3. Use area nova de malla 70/140 e area nova 140/70 para axustar o tamaño da area (o contido de barro da area do prototipo é do 11.42%):
① Do 16 ao 21 de xaneiro, un total de 4257 veces de moenda de area en cinco días, aproximadamente 4257 * 3/900 = 14 veces; o tamaño das partículas de cada ciclo cambia aproximadamente 0.26 (por moenda); polo tanto, a area de moldaxe o 16 de xaneiro O valor AFS é 49.15; a partir do 16 de xaneiro, cinco días de adición continua de 70/140 area nova para axustar o tamaño das partículas, 60 kg por fábrica, o valor AFS da area de moldaxe o 21 de xaneiro é de 52.84;
② Do 25 ao 27 de xaneiro, un total de 2165 tempos de moenda de area en tres días, aproximadamente 2165 * 3/900 = 7 ciclos; o tamaño do gran de cada ciclo cambia aproximadamente 0.22 (por moenda); polo tanto, o 24 de xaneiro AFS de area = 52.44, cando o tamaño das partículas da area de moldaxe alcanza os 52-53, a adición continua de 70/140 area nova ten pouco efecto sobre o sistema de area AFS; a partir do 26 de xaneiro, engádese 140/70 area nova durante tres días consecutivos para axustala e engádense 60 kg por cada moenda. 1 O 28, o AFS da area é de 54.
(Nota: ①A norma empresarial FAW estipula que a taxa de peneirado de 70/140 area de cuarzo 70,100,140 ≥80%, dos cales 70,100 peneira ≥60%; 140/70 area de cuarzo 70,100,140 taxa de peneira ≥80%, dos cales 100,140 taxa de peneira ≥60 % ②Cada volume de moenda é de 3 toneladas e estímase que o volume de area do sistema é de 900 toneladas)
4. Comparación do contido de barro e eliminación de po durante tres meses consecutivos:
Debido ao clima frío do norte de febreiro a marzo, o po da tubaxe de eliminación de po frío condensarase e solidificarase despois de que se elimine o po quente. Se a canalización non se limpa a tempo, produciranse bloqueos con frecuencia e a descarga diaria variará de 4 a 8 toneladas. O contido de barro do sistema de area fluctúa moito. Durante este período, o único xeito de aumentar a capacidade de eliminación de po e reducir o contido de barro é aumentando o volume de aire do equipo de eliminación de po e dragando as tubaxes;
Despois de entrar en abril, a temperatura aumentou gradualmente, o fenómeno de condensación e solidificación do po xa non apareceu, a cantidade de eliminación de po estabilizouse gradualmente, alcanzando unha descarga media de 7-8 toneladas ao día e reduciuse o rango de flutuación do contido de barro;
O contido de barro do sistema de area de moldaxe tamén pode reducirse engadindo nova area ou reducindo a adición de materiais auxiliares. As desvantaxes destes dous métodos explicaranse na conclusión da proba.
5. Conclusión da proba
1. Axuste a cantidade efectiva de accesorios de area
Os cristais de bentonita dananse ata certo punto por quecemento e a forza de unión húmida diminuirá obviamente despois de engadir auga e mesturar. Despois de quentar a maior temperatura e máis tempo, a estrutura cristalina da bentonita destrúese por completo e convértese en "arxila morta" sen forza de cohesión. O aumento do espesor de fundición, a baixa relación area-ferro, a alta temperatura de vertido e o longo tempo de arrefriamento aumentan a perda de combustión de bentonita.
O xeito máis directo de xulgar se o po de carbón efectivo na area de moldaxe é suficiente é observar a suavidade da superficie da fundición e se hai pegada de area. Parte do carbón da area vella queimase debido á calor do metal fundido derramado e é preciso repoñelo. Por outra banda, tamén hai que engadir materiais recentemente engadidos como area fresca, area de núcleo mixto e bentonita para acadar o nivel de carbón pulverizado efectivo. A cantidade total de carbón pulverizado engadido durante a mestura de area é a suma da perda de queima e a cantidade adicional adicional. (O carbón efectivo en po equivale ao aditivo efectivo no texto)
2. Axuste do tamaño da area:
O tamaño da partícula da area de moldaxe a alta presión é xeralmente de 50/140, mentres que o tamaño das partículas dos núcleos de area de resina é maioritariamente de 50/100 ou máis groso. A mestura excesiva de area do núcleo afectará ao engrosamento de toda a vella area mollada, o que aumentará a permeabilidade da area e desgastará a superficie do molde.
Para evitar que o tamaño da partícula da area de moldaxe se volva grosa, as partículas do sistema de eliminación de po pódense reciclar na area vella. Ou engade area nova e fina para axustar; como se menciona na fundición, cando o AFS da area de moldaxe alcanza os 48, axústase engadindo continuamente 70/140 ou 140/70 area nova; con todo, porque as pezas fundidas están rotas no núcleo do sistema de area A cantidade de area xa é grande. Se o tamaño das partículas da area de moldaxe non se engrosa nun grao insoportable, non se recomenda engadir unha cantidade tan grande de area nova continuamente, se non, afectará a outros indicadores de rendemento do sistema de area de moldaxe (contido de barro, cantidade efectiva e forza debido á cantidade excesiva de area nova). ) ter influencia en;
3. Axuste do contido de barro
O aumento do contido de barro fará que a permeabilidade da area de moldaxe diminúa e o fenómeno da "explosión de gas" ocorrerá durante o proceso de vertido e a fundición será eliminada debido á explosión e á area pegañenta. O contido de barro do sistema de area de moldaxe non debe ser demasiado alto; pódese reducir o contido de barro do sistema de area reducindo a cantidade de materiais auxiliares, pero a redución do contido efectivo de bentonita fará diminuír a resistencia da area de moldaxe e reducirase a capacidade de levantar e resistir a area; a dosificación efectiva de Diminución fará diminuír a capacidade antiadherente da area.
Se aumenta a cantidade de area nova engadida para axustar o contido de barro, primeiro calcule a cantidade de barro que producen os distintos materiais recentemente engadidos na area fundida e, a continuación, pode calcular a cantidade de area bruta que hai que engadir para facer o contido de barro de. a area de moldaxe cumpre co Regulamento do proceso.
Como se menciona no artigo, o contido de barro pode reducirse un 0.1% por cada 30 kg de area nova engadida na fundición; con todo, a adición excesiva de area nova non só causará desperdicio de custos, senón que tamén reducirá a proporción de area usada no sistema de area de moldaxe, o que reducirá o rendemento da area de moldaxe. , A area de moldaxe diverxe, o que afecta á capacidade da moldaxe de arena e o fenómeno de lavado de area prodúcese durante o proceso de fundición;
Polo tanto, o autor cre que é a mellor opción se se pode controlar o contido de barro do sistema de area axustando o equipo de eliminación de po.
En definitiva, o sistema de area estabilizado é capaz de producir pezas fundidas de alta calidade. A través deste concepto, debemos axustar continuamente o proceso de moldaxe de area segundo as condicións de produción cambiantes para satisfacer as necesidades de produción.
Mantén a fonte e o enderezo deste artigo para reimprimilos: Como garantir a estabilidade do sistema de area verde?
Minghe Compañía de Fundición a Presión dedícanse á fabricación e proporcionan pezas de fundición de calidade e alto rendemento (a gama de pezas de fundición a presión de metal inclúe principalmente Fundición a presión de parede delgada,Fundición a cámara quente,Fundición a cámara fría), Servizo redondo (servizo de fundición a presión,Cnc mecanizado,Fabricación de moldes, Tratamento de superficie). Calquera requirimento de fundición a presión de aluminio, magnesio ou fundición de Zamak / cinc e outros requisitos de fundición son benvidos para poñerse en contacto connosco.
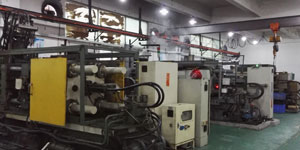
Baixo o control de ISO9001 e TS 16949, todos os procesos lévanse a cabo a través de centos de máquinas de fundición a presión avanzadas, máquinas de 5 eixes e outras instalacións, que van dende as blasters ata as lavadoras Ultra Sonic. Minghe non só ten equipos avanzados senón que tamén ten profesionais equipo de enxeñeiros, operadores e inspectores experimentados para facer realidade o deseño do cliente.
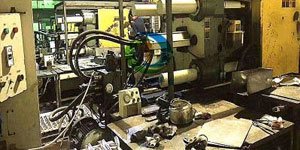
Fabricante por contrato de pezas fundidas. As capacidades inclúen pezas de fundición de aluminio a cámara fría de 0.15 libras. ata 6 libras, configuración rápida de cambio e mecanizado. Os servizos de valor engadido inclúen o pulido, vibración, desbarbado, granallado, pintura, revestimento, revestimento, montaxe e ferramentas. Entre os materiais traballados inclúense aliaxes como 360, 380, 383 e 413.
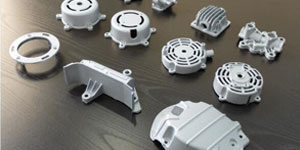
Servizos de enxeñaría simultánea de asistencia ao deseño de fundición por cinc. Fabricante a medida de pezas de fundición de cinc de precisión. Pódense fabricar pezas fundidas en miniatura, pezas fundidas de alta presión, pezas de molde de varias diapositivas, pezas de molde convencionais, pezas de moldaxe de pezas individuais e pezas de fundición independentes e pezas de fundición seladas. As pezas fundidas pódense fabricar en lonxitudes e anchuras de ata 24/0.0005 polgadas +/- XNUMX polgadas de tolerancia.
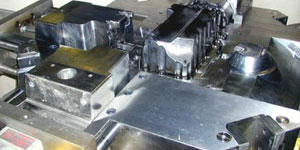
Fabricante certificado ISO 9001: 2015 de magnesio fundido a presión, as capacidades inclúen fundición a presión de magnesio de alta presión ata cámara quente de 200 toneladas e cámara fría de 3000 toneladas, deseño de ferramentas, pulido, moldeado, mecanizado, pintura en po e líquido, QA completo con capacidades CMM , montaxe, embalaxe e entrega.
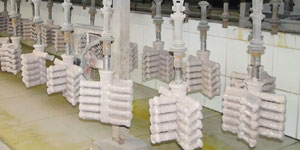
Certificado ITAF16949. Inclúe servizo de fundición adicional fundición de investimento,fundición de area,Fundición por gravidade, Fundición de escuma perdida,Fundición centrífuga,Fundición ao baleiro,Fundición permanente de moldesAs capacidades inclúen EDI, asistencia en enxeñaría, modelado sólido e procesamento secundario.
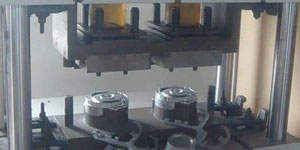
Industrias de fundición Estudos de casos de pezas para: coches, bicicletas, avións, instrumentos musicais, motos acuáticas, dispositivos ópticos, sensores, modelos, dispositivos electrónicos, caixas, reloxos, maquinaria, motores, mobles, xoias, discos, telecomunicacións, iluminación, dispositivos médicos, dispositivos fotográficos, Robots, esculturas, equipos de son, equipos deportivos, ferramentas, xoguetes e moito máis.
Que podemos axudarche a facer a continuación?
∇ Ir á páxina de inicio para China Fundición a Presión
→Pezas de fundición-Descubre o que fixemos.
→ Consellos recomendados sobre Servizos de fundición a presión
By Fabricante de fundición a presión Minghe | Categorías: Artigos útiles |material tags: Fundición de aluminio, Fundición de cinc, Fundición de magnesio, Fundición de titanio, Fundición de aceiro inoxidable, Fundición de latón,Fundición de bronce,Emisión de vídeo,Historia da empresa,Fundición en aluminio | Comentarios desactivados