"Alcalino" e "Magnesio" para mellorar o rendemento do pellet
Os gránulos oxidados teñen unha boa resistencia mecánica e propiedades metalúrxicas e convertéronse nunha carga indispensable de alta calidade para a fabricación de ferro de altos fornos. Non obstante, a falta de subministración doméstica de concentrado de magnetita fixo que moitas plantas siderúrxicas domésticas empregasen hematita importada para producir pelotas de óxido. En comparación cos gránulos de magnetita, os gránulos de hematita teñen unha alta temperatura de tostado e un rango estreito (1300 ~ 1350 ℃), e os gránulos teñen baixa resistencia á compresión. Ademais, os gránulos ácidos de hematita teñen malas propiedades metalúrxicas. Entre eles, a especularita pertence a un tipo importante de hematita, e o rendemento de tostado e as propiedades metalúrxicas dos gránulos son peores que os gránulos de hematita comúns.
Os investigadores realizaron moitas investigacións sobre como usar a hematita para producir pellets oxidados de alta resistencia. Os estudos demostraron que a adición de magnetita á hematita para preparar gránulos oxidados pode reducir efectivamente a temperatura de asado de precalentamento e aumentar a resistencia á compresión dos gránulos de asado precalentados; engadir fluxo para producir gránulos de hematita fundida tamén é unha solución.
As plantas domésticas de pellets usan xeralmente hematita e magnetita para producir pellets de alta resistencia, pero a medida que aumenta a proporción de hematita, o efecto da adición de magnetita debilita moito. Engadir fluxo de CaO para producir gránulos de fluxo pode obter maior resistencia mecánica e mellor reducibilidade a unha temperatura máis baixa, pero o rendemento de refluxo a alta temperatura é pobre e a expansión da redución é grave. Os primeiros estudos demostraron que a adición de MgO aos gránulos pode reducir a taxa de expansión de redución e mellorar o rendemento de refluxo a alta temperatura.
Na actualidade, hai relativamente poucos informes sobre o efecto da alcalinidade e o contido de MgO sobre a resistencia e as propiedades metalúrxicas dos gránulos de especularita, especialmente o efecto da alcalinidade e o MgO sobre as propiedades metalúrxicas dos gránulos. Polo tanto, este artigo Estudando os efectos da alcalinidade e o contido de MgO sobre a resistencia e as propiedades metalúrxicas dos gránulos de especularita ten un importante valor teórico para mellorar o tostado de gránulos e fortalecer a fabricación de ferro dos altos fornos.
Propiedades das materias primas e métodos de investigación
As materias primas empregadas neste experimento son a especularita brasileira, a bentonita, a caliza e a magnesita. Debido a que a especularita, a pedra calcaria e a magnesita brasileiras teñen un tamaño de partícula relativamente groso, son moídas ata o tamaño das partículas e a superficie específica necesaria para a produción de pellets cun molino de bolas no laboratorio. A especieite ten un alto grao de ferro, menos minerais de ganga e outras impurezas nocivas e é unha materia prima de pelotas de alta calidade. A caliza e a magnesita teñen un baixo contido de SiO2 e poucas outras impurezas nocivas. Son fluxos de calcio-magnesio de alta calidade.
O aglutinante usado na proba é bentonita a base de sodio de alta calidade e os indicadores son os seguintes: o contido de montmorillonita é do 92.76%, o volume de hinchazón é de 20 ml / g, a taxa de absorción de auga en 2 horas é do 342% e o contido de -0.074mm chega ao 100%.
A investigación experimental inclúe o proceso de mesturación, mestura, preparación de bólas verdes, secado de bolas verdes, asado precalentado de bólas secas e probas de rendemento de pellets asados. O contido de SiO2 dos gránulos acabados contrólase nun 3.0% ± 3.1% engadindo area de cuarzo finamente moída. A alcalinidade e o contido en MgO dos gránulos acabados axústanse engadindo pedra calcaria e magnesita e os efectos dos cambios na alcalinidade e contido en MgO sobre a resistencia á compresión, o grao de redución, a expansión de redución, a pulverización de baixa temperatura e a fusión suave de alta temperatura. investigan as características dos gránulos asados. Influencia.
Resultados da proba e análise de impacto
"O efecto da alcalinidade e do contido de MgO sobre a resistencia á compresión e a porosidade". A resistencia á compresión dos gránulos é un indicador importante que reflicte a presión que os gránulos poden soportar durante o proceso de transporte e almacenamento e no forno de redución. Os grandes fornos requiren que a resistencia á compresión dos pellets sexa superior a 2500 N / peza.
Baixo o contido natural de MgO, a resistencia á compresión dos gránulos aumenta primeiro co aumento da alcalinidade. Cando a alcalinidade aumenta a 0.2, a resistencia á compresión dos gránulos aumenta de 2400 N / peza de alcalinidade natural a 3,500 N / peza; Despois de chegar a 0.4, a resistencia á compresión dos gránulos xa non aumenta. Isto débese ao aumento da alcalinidade de CaO, Fe2O3 e SiO2, como a ferrita cálcica e o silicato cálcico. A fase líquida axeitada é favorable á recristalización da hematita, pero o exceso de fase líquida non favorece a mellora da resistencia á compresión dos gránulos. Baixo alcalinidade natural, a resistencia á compresión dos gránulos diminúe co aumento do contido en MgO. Isto débese a que a magnesita se descompón durante o precalentamiento e o asado dos gránulos, o que aumenta a porosidade dos gránulos.
Cando a alcalinidade e MgO traballan xuntos, baixo o mesmo contido de MgO, o efecto da alcalinidade sobre a resistencia á compresión dos gránulos calcinados é basicamente o mesmo que o efecto da alcalinidade sobre a resistencia á compresión dos gránulos baixo o contido natural de MgO, é dicir, a resistencia á compresión dos gránulos. A forza aumenta primeiro co aumento da alcalinidade. Despois de que a alcalinidade alcance un certo valor, a resistencia á compresión dos gránulos xa non aumenta significativamente; baixo a mesma alcalinidade, a resistencia á compresión dos gránulos diminúe co aumento do contido de MgO, que se debe ao contido de MgO A medida que aumenta, a porosidade dos gránulos aumenta e, ao mesmo tempo, o MgO entra na fase de escoria para aumentar o punto de fusión dos minerais da ganga, que ten un certo efecto obstaculizador na formación da fase líquida. Os resultados da proba mostran que cando a alcalinidade é superior a 0.2, a resistencia á compresión dos gránulos de especularita con diferente alcalinidade e contido en MgO pode alcanzar máis de 2500 N / peza.
A medida que aumenta a cantidade de fluxo, tamén aumentan os poros deixados pola descomposición do fluxo durante o asado de precalentamento. A adición de fundente non só afecta á composición química e á composición mineral dos gránulos, senón que tamén afecta á estrutura e á porosidade dos gránulos. Isto afectará á resistencia á compresión e ás propiedades metalúrxicas dos gránulos ata certo punto.
O efecto da alcalinidade e do contido de MgO no grao de redución. O grao de redución (RI) é un indicador importante para avaliar a tendencia e dificultade de eliminar osíxeno do mineral de ferro nas condicións de temperatura e atmosfera na zona de redución do alto forno. Os factores que afectan o grao de redución do mineral de ferro inclúen o tamaño das partículas, a porosidade, a composición e a estrutura mineral e a composición mineral de gangue.
O grao de redución de pelotas ácidas con alcalinidade natural e contido natural en MgO é baixo, só o 62.22%. Co aumento do contido de MgO, o grao de redución aumenta. Cando o contido de MgO é do 3.0%, o grao de redución dos gránulos pode chegar ao 68%; Cando o contido de MgO aumenta a alcalinidade, o grao de redución dos gránulos de especularita mellórase moito. Cando a alcalinidade aumenta a 1.2, o grao de redución dos gránulos aumenta ata o 72.82%. Isto débese a que a adición de pedra calcaria aumenta a porosidade dos gránulos e, ao mesmo tempo, o CaO reacciona con Fe2O3 para formar ferrita de calcio facilmente reducida.
Cando a alcalinidade e MgO actúan xuntos, baixo a mesma alcalinidade, o grao de redución dos gránulos de mirrorita aumenta co aumento do contido en MgO; baixo o mesmo contido de MgO, o grao de redución aumenta co aumento da alcalinidade.
Cando a alcalinidade alcanza o 1.2 e o contido de MgO aumenta ata o 3.0%, o grao de redución dos gránulos é de ata o 76.94%. Isto débese a que a magnesita tamén aumenta a porosidade dos gránulos durante o precalentamento e o tostado dos gránulos e o MgO pode aumentar o punto de fusión da fase de escoria e do corpo flotante, de xeito que non é doado fundir durante o proceso de redución, e os poros dos gránulos non se derriten. O material énchese para manter unha alta porosidade, o que favorece a difusión do gas.
O efecto da alcalinidade e do contido de MgO na redución da expansión.
Baixo o contido natural de MgO, a taxa de expansión de redución dos gránulos de especularita primeiro aumenta e despois diminúe, e a alcalinidade alcanza o valor máximo entre 0.4 e 0.6, e o valor máximo é do 32%.
Isto débese a que unha pequena parte do CaO engadido aos gránulos reacciona con Fe2O3 para producir ferrita cálcica e a maior parte entra na fase de escoria. Cando non se reduce, a fase de escoria está dominada polo sistema binario CaO-SiO2. Cando a alcalinidade está entre 0.4 e 0.6, é dicir, o contido de SiO2 na fase de escoria está entre o 62.5% e o 70%, que é o intervalo da composición binaria do punto eutéctico do metasilicato cálcico (CaOSiO2) e SiO2, e o seu baixo contido o punto eutéctico de temperatura é de 1436 ℃, pero en condicións redutoras, esta fase de escoria convértese nun sistema de escoria ternaria CaO-SiO2-FeO debido á adición de FeO. Neste sistema de escorias, a proporción de CaO e SiO2 permanece inalterada. O punto de fusión da fase de escoria aumenta bruscamente co aumento do contido en FeO. No sistema de escoria ternaria pura, pode chegar a 1093 ℃ e a fase de escoria de baixo punto de fusión só empeorará a redución e expansión dos gránulos.
Baixo alcalinidade natural, a taxa de expansión de redución de pelotas diminúe lixeiramente co aumento do contido de MgO, pero non é obvio. Isto débese á alcalinidade natural e á fase natural de escoria de pellets de MgO cun punto de fusión de 1700 ℃ cando o contido de SiO2 é do 90%. Coa adición de MgO, a fase de escoria está dominada polo sistema binario MgO-SiO2, pero a súa temperatura eutéctica a baixa temperatura tamén ten unha temperatura eutéctica baixa. 1543 ° C. Cando a alcalinidade e o MgO funcionan xuntos, o efecto da alcalinidade sobre a taxa de expansión de redución de pelotas é basicamente o mesmo que o contido natural de MgO baixo o mesmo contido de MgO. Cando se engade MgO, o punto de fusión da fase de escoria aumenta coa fusión de MgO na fase de escoria. Ao mesmo tempo, o punto de fusión da fase de escoria tamén aumenta o MgO na fase de escoria.
Polo tanto, baixo a mesma alcalinidade, aumentar o contido de MgO pode reducir a expansión da redución.
A expansión do volume da hematita nos gránulos oxidados redúcese a magnetita e floatita. Esta expansión é causada principalmente polo cambio da estrutura cristalina cando a hematita se reduce a magnetita. A taxa de expansión de redución dos gránulos está relacionada coa composición da ganga e coa capacidade da fase de escoria para soportar o estrés xerado pola redución de partículas de hematita.
A fase de escoria de alto punto de fusión non é doada de derreter durante o proceso de redución e manter unha alta resistencia pode limitar efectivamente a taxa de expansión de redución dos gránulos, mentres que a fase de escoria de baixo punto de fusión empeorará a expansión de redución dos gránulos.
A taxa de expansión de redución de pelotas por debaixo do 20% pertence ao intervalo de expansión normal e a alcalinidade de pelotas de especularita debe controlarse dentro do rango inferior a 0.2 ou superior ou igual a 1.0.
Non obstante, na produción industrial xeral, débese controlar a taxa de expansión de redución dos pelotas por baixo do 15%. Para os gránulos de especularita con alcalinidade natural que conteñen 3.0% ~ 3.1% de SiO2, a taxa de expansión de redución é inferior ao 15% e o grao de redución é só do 62.2%. Ao mellorar o grao de redución aumentando a alcalinidade, é necesario reducila só cando o grao de aumento a 1.0 e o contido de MgO ao 3.0%, ou a alcalinidade a 1.2 e o contido de MgO ≥1.0%, pode reducirse taxa inferior ao 15%.
O efecto da alcalinidade e do contido de MgO na pulverización por reducción de baixa temperatura. A pulverización por redución de baixa temperatura (RDI) reflicte a tendencia dos gránulos a producir po cando se reducen na parte superior do alto forno ou forno de eixe de redución directa nun rango de temperatura de 400 ° C a 600 ° C. A principal razón para a redución e pulverización de baixa temperatura é a expansión do volume e a distorsión do retículo causada pola conversión da estrutura cristalina cando a hematita se reduce a magnetita.
Hai tres métodos principais de unión formados cando os pellets se pre-quentan e tostan:
Recristalización de óxido de ferro, enlace de silicato e enlace de ferrita.
Entre eles, o enlace de recristalización da hematita é o máis común e forte, pero a hematita é extremadamente inestable en condicións redutoras, mentres que a fase de enlace do silicato pode manterse cando a hematita se reduce a magnetita. Cambio.
Polo tanto, é posible aumentar esta distribución uniforme e manter unha fase de unión estable baixo condicións de redución de baixa temperatura engadindo un fluxo, de xeito que se reduza a redución e pulverización a baixa temperatura de pelotas de espellita.
Os gránulos con alcalinidade natural e contido natural en MgO son principalmente unha consolidación de difusión en fase sólida de hematita, con menos fase de unión de silicatos. Polo tanto, prodúcese máis po durante a redución de baixa temperatura e o seu valor RDI-3.15 mm é ata 12.75. %. Baixo o contido natural de MgO, a alcalinidade aumentou a 0.2 e a velocidade de pulverización de baixa temperatura do pellet O valor RDI-3.15 mm diminuíu rapidamente ata o 0.52%; a alcalinidade continuou aumentando e o valor RDI-3.15 mm mantívose basicamente nun 0.5% aproximadamente. Isto débese a que a adición de CaO permite que os gránulos formen fases líquidas máis silicatas que sexan estables durante a redución de baixa temperatura durante o precalentamento e a calcinación, logrando así o propósito de reducir a redución a baixa temperatura e a pulverización dos gránulos.
Baixo alcalinidade natural, aumentando o contido de MgO, a redución de baixa temperatura e a taxa de pulverización dos gránulos, RDI-3.15 mm, caen todos por debaixo do 3.0%. Cando a alcalinidade e MgO funcionan xuntos, o valor RDI-3.15 mm dos gránulos na pulverización de redución de baixa temperatura é baixo. RDI-3.15 mm diminúe co aumento da alcalinidade e aumenta lixeiramente co aumento do contido en MgO. Isto débese a MgO Pode dificultar a formación de silicato en fase líquida.
O efecto da alcalinidade e do contido de MgO sobre as características do reflujo. As características de fusión dos gránulos poden reflectir a formación de gránulos na zona de fusión branda na parte inferior do alto forno e o seu rendemento na zona de fusión branda. As características de refluxo da carga teñen un maior impacto no funcionamento do alto forno. A temperatura de reblandecemento dos gránulos é baixa e o intervalo de refluxo é amplo e a permeabilidade ao aire da zona de refluxo na parte inferior do alto forno empeorará, o que non favorece a convección do gas redutor e a carga e afecta gravemente ao proceso de redución.
Os gránulos ácidos con alcalinidade natural e contido natural en MgO comezan a suavizarse a 1009 ° C e a temperatura de caída é de 1272 ° C. Con contido natural de MgO, a alcalinidade aumenta a 1.2, a temperatura de reblandecemento dos gránulos aumenta a 1034 ° C, o intervalo de reblandecemento e o intervalo de reblandecemento redúcense e a temperatura de goteo tamén aumenta a 1299 ° C. Cando a alcalinidade é 1.2, o aumento do contido de MgO pode aumentar a temperatura inicial de suavización e a temperatura de goteo. Cando o contido de MgO é do 1.0%, a temperatura de ablandamento da pelota subirá a 1072 ℃, a temperatura de goteo alcanzará os 1319 ℃, o contido de MgO seguirá aumentando e a temperatura de ablandamento da pelota non aumentará. .
As características de reflujo dos gránulos están afectadas principalmente polas fases líquidas de baixa fusión como a fusterita e a escoria producidas durante a redución. As malas características de refluxo a alta temperatura dos gránulos ácidos débense principalmente ao baixo punto de fusión da fase de escoria olivina rica en FeO durante o proceso de redución, e a adición de MgO pode aumentar o punto de fusión da fase de escoria. A formación dunha solución sólida cun alto punto de fusión tamén xogará un papel na mellora das características de refluxo de alta temperatura dos gránulos.
Mantén a fonte e o enderezo deste artigo para reimprimilos: "Alcalino" e "Magnesio" para mellorar o rendemento do pellet
Minghe Compañía de Fundición a Presión dedícanse á fabricación e proporcionan pezas de fundición de calidade e alto rendemento (a gama de pezas de fundición a presión de metal inclúe principalmente Fundición a presión de parede delgada,Fundición a cámara quente,Fundición a cámara fría), Servizo redondo (servizo de fundición a presión,Cnc mecanizado,Fabricación de moldes, Tratamento de superficie). Calquera requirimento de fundición a presión de aluminio, magnesio ou fundición de Zamak / cinc e outros requisitos de fundición son benvidos para poñerse en contacto connosco.
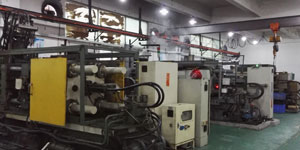
Baixo o control de ISO9001 e TS 16949, todos os procesos lévanse a cabo a través de centos de máquinas de fundición a presión avanzadas, máquinas de 5 eixes e outras instalacións, que van dende as blasters ata as lavadoras Ultra Sonic. Minghe non só ten equipos avanzados senón que tamén ten profesionais equipo de enxeñeiros, operadores e inspectores experimentados para facer realidade o deseño do cliente.
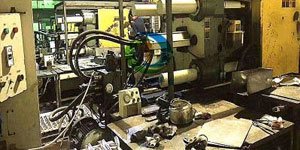
Fabricante por contrato de pezas fundidas. As capacidades inclúen pezas de fundición de aluminio a cámara fría de 0.15 libras. ata 6 libras, configuración rápida de cambio e mecanizado. Os servizos de valor engadido inclúen o pulido, vibración, desbarbado, granallado, pintura, revestimento, revestimento, montaxe e ferramentas. Entre os materiais traballados inclúense aliaxes como 360, 380, 383 e 413.
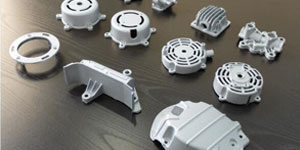
Servizos de enxeñaría simultánea de asistencia ao deseño de fundición por cinc. Fabricante a medida de pezas de fundición de cinc de precisión. Pódense fabricar pezas fundidas en miniatura, pezas fundidas de alta presión, pezas de molde de varias diapositivas, pezas de molde convencionais, pezas de moldaxe de pezas individuais e pezas de fundición independentes e pezas de fundición seladas. As pezas fundidas pódense fabricar en lonxitudes e anchuras de ata 24/0.0005 polgadas +/- XNUMX polgadas de tolerancia.
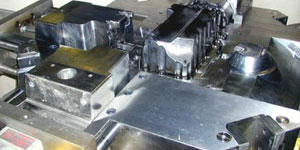
Fabricante certificado ISO 9001: 2015 de magnesio fundido a presión, as capacidades inclúen fundición a presión de magnesio de alta presión ata cámara quente de 200 toneladas e cámara fría de 3000 toneladas, deseño de ferramentas, pulido, moldeado, mecanizado, pintura en po e líquido, QA completo con capacidades CMM , montaxe, embalaxe e entrega.
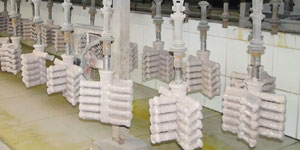
Certificado ITAF16949. Inclúe servizo de fundición adicional fundición de investimento,fundición de area,Fundición por gravidade, Fundición de escuma perdida,Fundición centrífuga,Fundición ao baleiro,Fundición permanente de moldesAs capacidades inclúen EDI, asistencia en enxeñaría, modelado sólido e procesamento secundario.
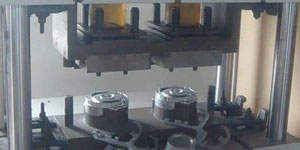
Industrias de fundición Estudos de casos de pezas para: coches, bicicletas, avións, instrumentos musicais, motos acuáticas, dispositivos ópticos, sensores, modelos, dispositivos electrónicos, caixas, reloxos, maquinaria, motores, mobles, xoias, discos, telecomunicacións, iluminación, dispositivos médicos, dispositivos fotográficos, Robots, esculturas, equipos de son, equipos deportivos, ferramentas, xoguetes e moito máis.
Que podemos axudarche a facer a continuación?
∇ Ir á páxina de inicio para China Fundición a Presión
→Pezas de fundición-Descubre o que fixemos.
→ Consellos recomendados sobre Servizos de fundición a presión
By Fabricante de fundición a presión Minghe | Categorías: Artigos útiles |material tags: Fundición de aluminio, Fundición de cinc, Fundición de magnesio, Fundición de titanio, Fundición de aceiro inoxidable, Fundición de latón,Fundición de bronce,Emisión de vídeo,Historia da empresa,Fundición en aluminio | Comentarios desactivados