Os puntos clave do novo tipo de carcasa de aceiro multifuncional de aliaxe de aluminio Fundición a presión
Con miras á tendencia de desenvolvemento dos motores de automóbiles cara a un peso e unha integración máis lixeiros, explícanse enfáticamente os puntos principais dun novo tipo de aceiro fundido a presión. Os puntos de tecnoloxía de deseño de fundición divídense en tres partes, utilizando diferentes métodos de vertido e novas tecnoloxías para deseñar produtos; desde os puntos de control do proceso de fundición a presión, contrólase cada factor que afecta á calidade do produto no proceso de produción para reducir as taxas de defectos do produto. A través destes dous aspectos do control, a taxa de cualificación do produto supera o 97% e a produción en masa é estable.
Co rápido desenvolvemento da industria do automóbil, os materiais, o deseño e fabricación de pezas presentan maiores requirimentos e a integración, o alto rendemento e o baixo custo convertéronse na tendencia de desenvolvemento. Tanto a bandeira de aceite como o bloque de cilindros inferior son partes importantes do motor do automóbil. Ao integrar o eixe de equilibrio do bloque de cilindros inferior e a función de recollida e filtrado da bandeira de aceite na mesma parte, o peso e o volume do motor redúcense efectivamente. Non obstante, debido á complexa estrutura e aos grandes cambios de espesor da parede, cómpre dividilo en diferentes produtos e procesalo por separado e despois combinalo e procesalo, o que resulta en dificultades na fabricación do produto.
A cubeta de aceite integrada dun motor estudada nesta materia contén tres pezas fundidas: o corpo da cubeta de aceite, a tapa do rodamento e unha tapa do rodamento. Usando material de aleación modificado A380, o espesor medio da parede da fundición é de 3 mm, o espesor mínimo da parede é de 2.5 mm e a masa do branco é de 10.74 kg. É necesario que a cavidade interna estea libre de fugas por debaixo de 300 kPa e o paso do aceite non se filtra a 600 kPa e a temperatura supera os 60 ℃. Fuga, utilizada en motores de 1.5 T, cunha produción anual de 400,000 pezas, que é unha fundición típica de aceiro.
Puntos técnicos do deseño de fundición a presión
1.1 Deseño do corredor
A fundición 1 adopta un deseño de vertedura a tres caras, pero céntrase na vertedura global por un dos lados, como se mostra na figura 1. Como o produto é longo (a lonxitude de arriba e abaixo alcanza os 437.2 mm), o deseño de vertedura a tres caras pode aliviar eficazmente o problema do proceso longo, para encher o produto en diferentes áreas. Non obstante, tendo en conta que o espesor total da parede do produto é máis groso e hai moitas insercións levantadas na posición de vertedura, para evitar que se bloquee a fluidez do aluminio fundido, refórzase o recheo dun lado e a sección transversal a área estreitase gradualmente no seu conxunto para acelerar o fluxo do aluminio fundido. Deseño sprue.
A fundición 2 é unha tapa de rodamento, cunha forma relativamente sinxela, só as dúas ranuras de aceite do eixe de balance son grosas. Baseado no patrón de fluxo simple do aluminio fundido, para aforrar custos e aumentar a velocidade de saída efectiva do aluminio fundido, adóptase un esquema de vertido dun só lado e a porta colócase na zona de espesor da parede para alimentarse, como mostrado na Figura 2.
Casting 3 é unha cuberta de tella de eixe de equilibrio cunha parte máis pequena (tamaño 63 mm) × 15 mm × Adóptase o deseño dunha cavidade e oito moldes para encher e verter, como se mostra na figura 3.
1.2 Método de escape
Para a fundición complexa 1 úsase un alto baleiro para o escape. Fundición 2, empregando un bloque de escape tipo "lavabo" normal. Casting 3 adopta directamente a bolsa de escoria e a canle de escape do núcleo do molde na cola da bolsa de escoria. Os principais puntos da tecnoloxía de escape de fundición 1 son aquí resaltados.
Dado que os pasos de aceite de alta presión e os filtros de aceite dos moldes están concentrados na cola de auga, o efecto de escape da cola de auga é o factor clave que determina a calidade interna destes lugares. A fundición 1 usa un escape de alto baleiro para reducir a presión do aire na zona de presión negativa da cola de auga da fundición. Primeiro de todo, o volume do tanque de baleiro debe seleccionarse ≥ 800 L (800 L aquí é máis de 10 veces o volume do molde que contén a cavidade e a artesa) para formar rapidamente a canle de presión negativa. En segundo lugar, a tubaxe que conecta o molde e a máquina de baleiro debe estar selada e hermética e o grao de baleiro da tubaxe debe manterse dentro de 2 Pa. están revestidos con selante. Despois de pechar o molde, o baleiro da cavidade debe manterse dentro de 000 Pa. Finalmente, escolla a mellor produción do punzón selado ou use a versión ampliada do punzón para aumentar a área de selado do punzón e aliviar efectivamente a fuga de aire á cavidade.
1.3 Temperatura do molde
Debido ás características do alto baleiro, o aluminio fundido non se enche completamente de acordo co estado teórico do fluído (ver a Figura 4) e o aluminio fundido é fácil de solidificar rapidamente en certos lugares cando é aspirado nel, provocando defectos de fundición a presión. como poros de fundición a presión, buratos de contracción e fendas. O produto desta fundición 1 comeza a aspirar cando o punzón se move á posición de 410 mm (a plenitude do líquido de aluminio alcanza o requisito do 70%) e pecha o baleiro á posición de 540 mm. Tempo), o trazo ao baleiro é de 130 mm e o tempo é de 0.874 s. Nun período de tempo tan curto, debe asegurarse de que o líquido de aluminio extraído non se solidifique nunha posición importante na cola da auga con antelación. Polo tanto, a temperatura do molde nestas posicións contrólase en 220 ℃ e 180 ℃ respectivamente usando unha máquina de temperatura do aceite. A temperatura elevada do molde e a maior liquidez do aluminio fundido son a clave para garantir a calidade interna destes dous lugares importantes.
Os moldes 2 e 3 teñen unha estrutura relativamente sinxela, unha distancia de recheo curta e fáciles de formar. Non requiren unha alta temperatura do molde, sempre que a temperatura da superficie do molde sexa alta e o produto non se volva negro.
1.4 Opcións de refrixeración do molde
Esta fundición 1 utiliza tecnoloxía de refrixeración superpunta e tecnoloxía de abastecemento de auga intermitente. Dado que a produción de fundición precisa manter unha temperatura máis elevada e hai máis bocas de inserción no lado do molde móbil, é necesario asegurarse de que a alta temperatura non só se asegura, senón tamén que as insercións levantadas non formarán xuntas quentes e causarán rachaduras por retracción e outros defectos. O proceso de corte realízase para cada inserto e o refrixeración puntual é conducido ao interior do inserto. O equipo periférico síncrono usa un método de abastecemento de auga intermitente. Durante a fase de solidificación do produto, a electroválvula ábrese para arrefriar o produto localmente. Isto non só obtén unha temperatura máis alta, senón que tamén obtén un bo efecto de arrefriamento. O proceso de refrixeración superpunto está deseñado para agullas de núcleo de fundición a presión, como mostra a frecha da figura 1. Unha agulla de 4 mm no medio da área de espesor da parede provocará directamente a contracción. O deseño de refrixeración superpunto utilízase para a agulla de 4 mm, que pode resolver o problema dos poros do burato roscado. Do mesmo xeito, noutros puntos moi quentes, úsase o deseño de agulla fría superpunto onde se pode expulsar a agulla, o que alivia moito os problemas de queimaduras, estomas e agullas rotas. O axuste do tempo de refrixeración superpunto e subministro de auga intermitente debe ter en conta o espesor da parede do burato perforado do material e a súa situación. Polo tanto, as agullas frías nestas diferentes áreas deben controlarse por zonas.
A fundición 2 só ten un orificio de ranura de aceite de 4 mm no medio do eixe de equilibrio e un furado de parafuso de Φ8 mm na entrada de alimentación, que usa un control de frío superpunto. Debido a que despois de rastrexar o líquido de aluminio, formarase unha canle solta entre as áreas de espesor da parede media, débese empregar unha agulla fría de punto excesivo para aumentar a forza a densa capa ao redor do estenopeico, cun atraso de 1 s e arrefriado durante 10 s. As 16 agullas pequenas de Φ8 mm en fundición 3 usan un control de frío superpunto para manter o espesor da densa capa preto do estenopeico.
1.5 Selección de tecnoloxía de extrusión local
O pasador de extrusión local pode resolver rapidamente a contracción na área de espesor da parede e é amplamente utilizado no campo da fundición a presión. A análise das xuntas quentes do fluxo do molde móstrase na figura 5. Hai moitas xuntas quentes na fundición 1 e a posición dos pasadores de extrusión debe estar razoablemente disposta. En primeiro lugar, elimina os nodos quentes que se poden eliminar usando a agulla fría e, en segundo lugar, elimina os nodos quentes que non están en posicións clave. Para rematar, cómpre considerar a disposición do cilindro do pasador de presión no espazo interno do molde. Xeralmente disponse nun punto onde a estrutura é complicada e se evita a fuga de aire.
Puntos clave do control do proceso de fundición a presión
2.1 Control do fluxo de pulverización durante a fundición a presión
Durante o proceso de fundición a presión, o caudal de pulverización mídese por separado mediante os moldes fixos e móbiles, o molde móbil contrólase a 3 200 ml e o molde fixo contrólase a 2 200 ml. Ademais, os valores de desviación superior e inferior configúranse por separado para os caudais de molde dinámicos e fixos. Dado que o caudalímetro electromagnético seleccionado ten unha precisión de 50 mL, a desviación de axuste é de ± 200 mL e 200 mL é o valor real medido despois de que se reduza unha pistola de pulverización. Durante o proceso de produción, se se supera o valor de desviación, emitirase un sinal de alarma directamente para deter o ciclo de produción de fundición a presión. Polo tanto, pode evitar de xeito efectivo que se bloquee a pulverización debido á pistola de pulverización, o que pode provocar pegadas e queimaduras do molde.
2.2 Control de procesos da temperatura do aluminio fundido
Dado que o efecto de conservación da calor do forno de retención é bo, pero a velocidade de calefacción é máis lenta que a do forno cuantitativo, cómpre controlar a temperatura de entrada do aluminio fundido. A temperatura de fundición do aluminio fundido é de 675 ± 10 ° C, polo que a temperatura de entrada do aluminio fundido no cucharón de transporte debe manterse por encima dos 700 ° C. A alimentación por debaixo desta temperatura afectará o estado de fluxo do aluminio fundido durante o proceso de recheo, o que provocará un aumento da proporción de poros nos lugares locais. Engadir materiais por riba de 730 ℃ provocará unha grave queimadura e pegado de aluminio na superficie do molde, o que afectará á calidade do aspecto da fundición. Configure a alarma de temperatura do aluminio fundido para o forno de suxeición. Se a temperatura de vertido non está dentro do intervalo, o forno de alarma alarmará e deterá o ciclo de produción de fundición a presión, o que pode evitar efectivamente os defectos causados pola desviación de temperatura do aluminio fundido.
2.3 Control do baleiro
Dado que o molde de fundición 1 está selado cunha cinta de selar móbil fixa e móbil, todos os pasadores do dedal e do núcleo péchanse aplicando selador, e o canalón tamén é un canalón integral, pero o punzón non usa un punzón de selado especial, senón que usa un perforador de placa de extensión (estendido a 150 mm). Nunha condición tan pechada, activarase unha alarma cando o grao de baleiro estea excedido de 4 kPa (4 kPa é un valor de alarma empírico establecido segundo a alta taxa de paso durante o proceso de produción) e o grao de baleiro xeralmente rolda os 2.3 k Pa. Os valores de limpeza e obstrución adoitan estar preto de 101 kPa e o valor de alarma establecido é de 90 kPa (90 kPa configúrase segundo o ciclo de limpeza do depósito de filtro na fábrica). Ao final dun ciclo de limpeza, o depósito do filtro da válvula de baleiro debe limparse a tempo. Se non se limpa afectará o efecto de aspiración. O valor de axuste do tanque de baleiro é de 1 kPa, que xeralmente está entre 2.2 e 400 Pa. Sempre que se supere o valor requirido, emitirase unha alarma e a máquina de fundición a presión será apagada.
2.4 Seguimento dos parámetros reais de inxección
A máquina de fundición a presión adopta o modelo doméstico Ube 1650T. Ademais do seu propio sistema de control de parámetros de máquina de fundición a presión, tamén usa un sistema de trazabilidade de código bidimensional (chamado sistema MES na fábrica) para conectar a máquina de fundición a presión e o equipo auxiliar periférico para que o sistema MES poida ler parámetros de produción de cada molde en tempo real e retroalimentalos á nube para a súa comparación na nube (o valor de comparación da nube introdúcese na nube con antelación segundo se precise e saen diferentes valores de rango segundo o logro real de diferentes Por exemplo, a velocidade lenta é de ± 0.05 m / s, a velocidade alta é de ± 3 m / s, etc., ver táboa 2), os produtos que superen o rango despois da comparación serán bloqueados polo sistema e xulgados como non cualificados . Cloud Big Data tamén calcula regularmente a relación en tempo real entre a obsolescencia do produto e os cambios de parámetros en función do volume de datos actualizado. Descubra as razóns das fluctuacións na taxa de chatarra nun período de tempo e mellore a taxa cualificada de mantemento dos produtos. Hai flutuacións no proceso de produción de fundición a presión, que pode descubrir rapidamente os puntos do problema e promover de forma efectiva un ciclo virtuoso no acto.
2.5 Control do transporte de auga fundida a presión
Ao comezo do transporte de auga, cada liña usa unha electroválvula para controlar o tempo de refrixeración directa ou o transporte ordinario de auga fría. A presión da auga é de 0.4 MPa e a temperatura da auga é de 30 water de auga pura. Con excepción da artesa, manguito de material, punzón, cono dividido e manguito de material forxado frío que normalmente están abertos e arrefriados directos, o resto de arrefriamento directo (barreiras de auga) e refrixeración de gran punto están controlados por electroválvula, atraso 3 s, arrefriamento 15 s para garantir a temperatura do molde. Todas as agullas, de Φ4 mm a Φ14 mm (o tubo central de Φ1.5 mm a Φ5.5 mm) están controladas por frío superpunto, a presión de transporte de auga fría superpunta é de 10 MPa e a temperatura de transporte de auga é 10 ℃ (aquí a temperatura non se pode establecer demasiado baixa, demasiado baixa quitará máis calor, pero pode provocar roturas de agullas), cada grupo de agullas súper frías do mesmo tamaño non excede de 8 (máis de 8 agullas superan diámetro do diámetro do tubo de conexión G1 / 2), todas as agullas combínanse nun total de 6 grupos, agás a agulla fría de punto de mm4 mm, o tempo de atraso é de 5 s e o arrefriamento de 13 s e o de Φ4 A agulla fría de punto mm axústase a 4 s e o tempo de arrefriamento é de 13 s para dirixirse ao campo de temperatura do molde. Na zona que hai que arrefriar rapidamente, reduce a aparición de puntos quentes. Non só garante o equilibrio e a preservación da calor da temperatura do molde, senón que tamén elimina os puntos quentes locais e garante a calidade do produto.
3. A calidade da nova tixola multifuncional. Os tres produtos prodúcense en dúas máquinas diferentes e a produción diaria é de ata 980 pezas / día, 1,500 pezas / día e 12,000 pezas / día desde a fundición 1 ata a fundición 3. A taxa de aprobación global dos tres produtos ata o a montaxe final é do 97%. A figura 8 é unha imaxe do aspecto dos moldes 1, 2 e da calidade interna dos moldes 1, 2 e 3.
4 Conclusión
- O deseño e os puntos técnicos deste novo tipo de pota de aceite son o uso flexible do baleiro, refrixeración puntual, extrusión, balance de temperatura do molde e outros procesos baixo 3 modos de vertido e escape diferentes, e o procesamento final combínase nun único compoñente.
- O punto clave do control de fundición a presión é profundar continuamente e controlar os factores que afectan a inestabilidade da calidade do produto, para lograr un proceso de produción estable.
- Despois de superar o deseño do plan preliminar e a identificación e análise dos puntos técnicos, adóptase o control do proceso que tende a ser un seguimento automatizado, de xeito que o qu
Mantén a fonte e o enderezo deste artigo para reimprimilos: Os puntos clave do novo tipo de carcasa de aceiro multifuncional de aliaxe de aluminio Fundición a presión
Minghe Compañía de Fundición a Presión dedícanse á fabricación e proporcionan pezas de fundición de calidade e alto rendemento (a gama de pezas de fundición a presión de metal inclúe principalmente Fundición a presión de parede delgada,Fundición a cámara quente,Fundición a cámara fría), Servizo redondo (servizo de fundición a presión,Cnc mecanizado,Fabricación de moldes, Tratamento de superficie). Calquera requirimento de fundición a presión de aluminio, magnesio ou fundición de Zamak / cinc e outros requisitos de fundición son benvidos para poñerse en contacto connosco.
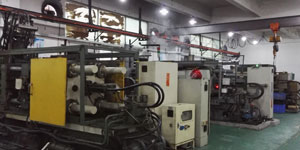
Baixo o control de ISO9001 e TS 16949, todos os procesos lévanse a cabo a través de centos de máquinas de fundición a presión avanzadas, máquinas de 5 eixes e outras instalacións, que van dende as blasters ata as lavadoras Ultra Sonic. Minghe non só ten equipos avanzados senón que tamén ten profesionais equipo de enxeñeiros, operadores e inspectores experimentados para facer realidade o deseño do cliente.
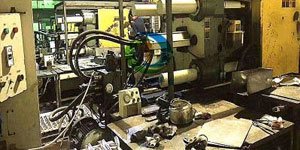
Fabricante por contrato de pezas fundidas. As capacidades inclúen pezas de fundición de aluminio a cámara fría de 0.15 libras. ata 6 libras, configuración rápida de cambio e mecanizado. Os servizos de valor engadido inclúen o pulido, vibración, desbarbado, granallado, pintura, revestimento, revestimento, montaxe e ferramentas. Entre os materiais traballados inclúense aliaxes como 360, 380, 383 e 413.
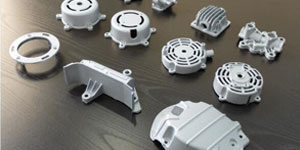
Servizos de enxeñaría simultánea de asistencia ao deseño de fundición por cinc. Fabricante a medida de pezas de fundición de cinc de precisión. Pódense fabricar pezas fundidas en miniatura, pezas fundidas de alta presión, pezas de molde de varias diapositivas, pezas de molde convencionais, pezas de moldaxe de pezas individuais e pezas de fundición independentes e pezas de fundición seladas. As pezas fundidas pódense fabricar en lonxitudes e anchuras de ata 24/0.0005 polgadas +/- XNUMX polgadas de tolerancia.
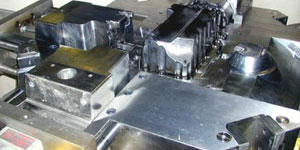
Fabricante certificado ISO 9001: 2015 de magnesio fundido a presión, as capacidades inclúen fundición a presión de magnesio de alta presión ata cámara quente de 200 toneladas e cámara fría de 3000 toneladas, deseño de ferramentas, pulido, moldeado, mecanizado, pintura en po e líquido, QA completo con capacidades CMM , montaxe, embalaxe e entrega.
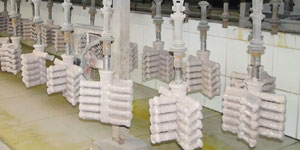
Certificado ITAF16949. Inclúe servizo de fundición adicional fundición de investimento,fundición de area,Fundición por gravidade, Fundición de escuma perdida,Fundición centrífuga,Fundición ao baleiro,Fundición permanente de moldesAs capacidades inclúen EDI, asistencia en enxeñaría, modelado sólido e procesamento secundario.
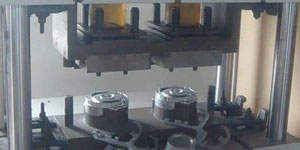
Industrias de fundición Estudos de casos de pezas para: coches, bicicletas, avións, instrumentos musicais, motos acuáticas, dispositivos ópticos, sensores, modelos, dispositivos electrónicos, caixas, reloxos, maquinaria, motores, mobles, xoias, discos, telecomunicacións, iluminación, dispositivos médicos, dispositivos fotográficos, Robots, esculturas, equipos de son, equipos deportivos, ferramentas, xoguetes e moito máis.
Que podemos axudarche a facer a continuación?
∇ Ir á páxina de inicio para China Fundición a Presión
→Pezas de fundición-Descubre o que fixemos.
→ Consellos recomendados sobre Servizos de fundición a presión
By Fabricante de fundición a presión Minghe | Categorías: Artigos útiles |material tags: Fundición de aluminio, Fundición de cinc, Fundición de magnesio, Fundición de titanio, Fundición de aceiro inoxidable, Fundición de latón,Fundición de bronce,Emisión de vídeo,Historia da empresa,Fundición en aluminio | Comentarios desactivados