Os factores que inflúen no tratamento térmico das forxadas metálicas
Na produción de forxa, ademais de garantir a forma e o tamaño requiridos da forxa, tamén debe cumprir os requisitos de rendemento da peza durante o uso. Usando parámetros de proceso e tecnoloxía de forxa razoables, a organización e estrutura das materias primas poden mellorarse a través dos seguintes aspectos:
- Rompe os cristais columnares, mellora a macrosegregación, cambia a estrutura como fundida na estrutura forxada e, baixo as condicións adecuadas de temperatura e tensión, solda os ocos internos para aumentar a densidade do material;
- O lingote forxase para formar unha estrutura de fibra e úsanse máis laminados, extrusión e forjado por matriz para obter unha distribución razoable da dirección da fibra para a forxa;
- Controlar o tamaño e uniformidade dos grans de cristal;
- Mellorar a distribución da segunda fase (como carburos de aliaxe en ledeburita ríxida);
- A estrutura refórzase mediante deformación ou transformación en fase de deformación.
Debido á mellora da estrutura mencionada, tamén se melloraron a plasticidade, a resistencia ao impacto, a resistencia á fatiga e a durabilidade dos forxados e, a continuación, a través do tratamento térmico final das pezas, unha boa combinación de dureza, resistencia e plasticidade requirida por pódense obter as partes. actuación.
Se o proceso de forxa usado non é razoable, pode producir defectos de forxa, incluídos defectos de superficie, defectos internos ou rendemento non cualificado, que afectarán a calidade do procesamento dos procesos posteriores, e algúns afectarán seriamente o rendemento dos forxados e reducirán a calidade dos produtos acabados. . A vida útil da batería pode incluso poñer en perigo a seguridade.
A influencia da estrutura de forxa na estrutura e propiedades despois do tratamento térmico final maniféstase principalmente nos seguintes aspectos:
- Defectos estruturais non mellorables: aceiros inoxidables resistentes ao calor austeníticos e ferríticos, aliaxes de alta temperatura, aliaxes de aluminio, aliaxes de magnesio, etc., materiais que non teñen transformación isomérica durante a calefacción e refrixeración, así como algunhas aliaxes de cobre e os defectos estruturais xerados durante o proceso de forxa non se poden mellorar mediante tratamento térmico.
- Defectos organizativos que se poden mellorar: estrutura de gran groso e de Widmanstatten en xeral forxados de aceiro estrutural sobrequentados, lixeiros carburos de rede causados por un arrefriamento inadecuado de aceiros hipereutectoides e aceiros do rodamento durante o tratamento térmico posterior á forxa. Pódese obter unha estrutura e un rendemento satisfactorios despois do final tratamento térmico da forxa (3) Os defectos organizativos que son difíciles de eliminar mediante o tratamento térmico normal: como o groso groso de baixo aumento, o aceiro inoxidable 9Cr18, os dous carburos de H13, etc., requiren normalización a alta temperatura, normalización repetida, descomposición a baixa temperatura, recocido por difusión a alta temperatura e outras medidas a mellorar.
- Defectos de organización que non poden ser eliminados polo proceso xeral de tratamento térmico: fracturas graves de pedra e cristais, queimadura excesiva, bandas de ferrita en aceiro inoxidable, mallas de carburo e bandas de aceiro de ferramentas de aliaxe de ledeburita, etc. incluso falla.
- Defectos da microestrutura que se desenvolverán durante o tratamento térmico final: por exemplo, a estrutura de gran groso na forxa de aceiro estructural de aliaxe, se o tratamento térmico despois da forxa non se mellora, a miúdo provoca martensita despois do carbono, nitruración e temperado A agulla é grosa e a actuación non está cualificada; os carburos de grosas bandas de aceiro de alta velocidade a miúdo causan rachaduras durante o apagado.
- Se a calefacción é inadecuada, por exemplo, a temperatura de calefacción é demasiado alta e o tempo de calefacción é demasiado longo, causará defectos como a descarburación, o sobrecalentamento e a queima.
- Durante o proceso de arrefriamento despois da forxa, se o proceso é inadecuado, pode provocar rachaduras de arrefriamento, manchas brancas, etc., que se poden rachar durante o tratamento térmico.
Cales son os efectos do corte na calidade das pezas tratadas térmicamente?
- No estado de apagado e templado, recocido e normalización da peza de traballo, a dureza é inferior a 45HRC e a calidade da peza, incluído o acabado superficial, a tensión residual, o permiso de mecanizado e a eliminación da capa de carbono descarburado da superficie. afectados polo proceso de corte. Obviamente, non causará un cambio no rendemento potencial da peza.
- O procesamento de pezas de aceiro endurecido ou pezas tamén se denomina procesamento duro. A dureza das pezas é de ata 50 ~ 65HRC. Os materiais inclúen principalmente aceiro temperado normal, aceiro troquelado, aceiro rodante, aceiro laminado e aceiro de alta velocidade, etc. O impacto do corte é máis evidente. Factores como a xeración e condución de calor de corte, fricción de alta velocidade e desgaste durante o proceso de corte causarán un certo grao de dano á superficie mecanizada. A integridade da superficie mecanizada durante o corte duro inclúe principalmente a textura da superficie, dureza, rugosidade da superficie, precisión dimensional, distribución de tensións residuais e xeración de capa branca.
A dureza da superficie mecanizada aumenta co aumento da velocidade de corte e diminúe co aumento da velocidade de avance e da cantidade de corte. E canto maior sexa a dureza da superficie mecanizada, maior será a profundidade da capa endurecida. Os resultados mostran que a tensión de compresión residual uniforme na superficie da peza despois do corte duro, mentres que a tensión máxima de compresión da peza despois da moenda concéntrase principalmente na superficie da peza.
Canto maior sexa o radio de ángulo obtuso da ferramenta, maior será o valor da tensión de compresión residual; canto maior sexa a dureza da peza, maior será o valor da tensión residual por compresión. A dureza da peza ten unha grande influencia na integridade superficial da peza. Canto maior sexa a dureza da peza, máis propicio para a formación de tensión de compresión residual.
Outro factor importante que afecta á calidade da superficie do corte duro é a formación de capas brancas. A capa branca é unha estrutura formada polo proceso de corte duro. Ten características de desgaste únicas: por un lado, ten unha dureza elevada e unha boa resistencia á corrosión; por outra banda, mostra unha alta fraxilidade, que é fácil de provocar un fracaso precoz do espallamento. Pode incluso rachar despois de colocalo nunha etapa despois do procesamento. Ao cortar aceiro endurecido AISIE52100 con ferramentas de cerámica e PCBN nun torno CNC de alta rixidez, comprobouse que as capas superficiais e sub-superficiais da peza cambiaron na súa microestrutura. A microestrutura está composta por unha capa branca sen temperar e unha capa negra sobre temperada.
Na actualidade, recoñeceuse por unanimidade a opinión de que a capa branca é unha estrutura de martensita e a principal disputa radica na estrutura fina da capa branca. Unha visión é que a capa branca é o resultado dun cambio de fase e está composta por martensita de gran fino formada por un quecemento rápido e un arrefriamento repentino do material durante o proceso de corte. Outra visión é que a formación da capa branca é só un termo de mecanismo de deformación, que é só unha martensita non convencional obtida por deformación plástica.
Mantén a fonte e o enderezo deste artigo para reimprimilos:Os factores que inflúen no tratamento térmico das forxadas metálicas
Minghe Compañía de Fundición a Presión dedícanse á fabricación e proporcionan pezas de fundición de calidade e alto rendemento (a gama de pezas de fundición a presión de metal inclúe principalmente Fundición a presión de parede delgada,Fundición a cámara quente,Fundición a cámara fría), Servizo redondo (servizo de fundición a presión,Cnc mecanizado,Fabricación de moldes, Tratamento de superficie). Calquera requirimento de fundición a presión de aluminio, magnesio ou fundición de Zamak / cinc e outros requisitos de fundición son benvidos para poñerse en contacto connosco.
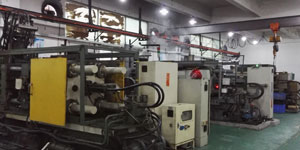
Baixo o control de ISO9001 e TS 16949, todos os procesos lévanse a cabo a través de centos de máquinas de fundición a presión avanzadas, máquinas de 5 eixes e outras instalacións, que van dende as blasters ata as lavadoras Ultra Sonic. Minghe non só ten equipos avanzados senón que tamén ten profesionais equipo de enxeñeiros, operadores e inspectores experimentados para facer realidade o deseño do cliente.
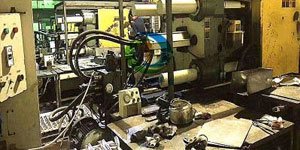
Fabricante por contrato de pezas fundidas. As capacidades inclúen pezas de fundición de aluminio a cámara fría de 0.15 libras. ata 6 libras, configuración rápida de cambio e mecanizado. Os servizos de valor engadido inclúen o pulido, vibración, desbarbado, granallado, pintura, revestimento, revestimento, montaxe e ferramentas. Entre os materiais traballados inclúense aliaxes como 360, 380, 383 e 413.
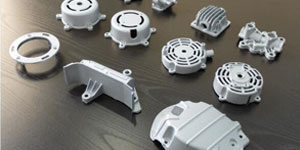
Servizos de enxeñaría simultánea de asistencia ao deseño de fundición por cinc. Fabricante a medida de pezas de fundición de cinc de precisión. Pódense fabricar pezas fundidas en miniatura, pezas fundidas de alta presión, pezas de molde de varias diapositivas, pezas de molde convencionais, pezas de moldaxe de pezas individuais e pezas de fundición independentes e pezas de fundición seladas. As pezas fundidas pódense fabricar en lonxitudes e anchuras de ata 24/0.0005 polgadas +/- XNUMX polgadas de tolerancia.
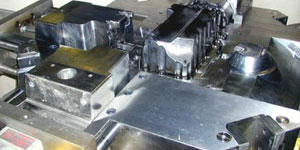
Fabricante certificado ISO 9001: 2015 de magnesio fundido a presión, as capacidades inclúen fundición a presión de magnesio de alta presión ata cámara quente de 200 toneladas e cámara fría de 3000 toneladas, deseño de ferramentas, pulido, moldeado, mecanizado, pintura en po e líquido, QA completo con capacidades CMM , montaxe, embalaxe e entrega.
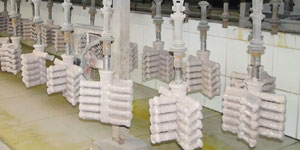
Certificado ITAF16949. Inclúe servizo de fundición adicional fundición de investimento,fundición de area,Fundición por gravidade, Fundición de escuma perdida,Fundición centrífuga,Fundición ao baleiro,Fundición permanente de moldesAs capacidades inclúen EDI, asistencia en enxeñaría, modelado sólido e procesamento secundario.
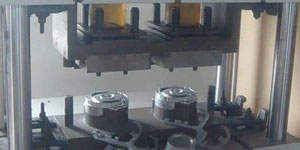
Industrias de fundición Estudos de casos de pezas para: coches, bicicletas, avións, instrumentos musicais, motos acuáticas, dispositivos ópticos, sensores, modelos, dispositivos electrónicos, caixas, reloxos, maquinaria, motores, mobles, xoias, discos, telecomunicacións, iluminación, dispositivos médicos, dispositivos fotográficos, Robots, esculturas, equipos de son, equipos deportivos, ferramentas, xoguetes e moito máis.
Que podemos axudarche a facer a continuación?
∇ Ir á páxina de inicio para China Fundición a Presión
→Pezas de fundición-Descubre o que fixemos.
→ Consellos recomendados sobre Servizos de fundición a presión
By Fabricante de fundición a presión Minghe | Categorías: Artigos útiles |material tags: Fundición de aluminio, Fundición de cinc, Fundición de magnesio, Fundición de titanio, Fundición de aceiro inoxidable, Fundición de latón,Fundición de bronce,Emisión de vídeo,Historia da empresa,Fundición en aluminio | Comentarios desactivados